1 Overview of the Article
The article will give an overview of a typical natural gas compression facility. The article will also cover other ancillaries in a gas compression facility. Though gas compression facilities have similar functional equipment, there are usually differences in configuration and equipment type, therefore there might be differences between the equipment described in this article and other facilities.
2 Introduction
Gas is a substance (element or compound) existing in a free expanding state, it freely expands to fill an entire container. Gas molecules are far apart, this implies they can be compressed to a smaller volume.
Various elements and compounds exist in a gaseous state including natural gas, oxygen, and hydrogen.
Amongst these gaseous substances, Natural gas is one of the most important because of its wide applications. It is a source of fuel for electricity generation, cars, cooking, heating, etc.
Before Natural gas is put into use, it must undergo series of processing to rid the gas of impurities. These impurities may include water, sulfur dioxide, and hydrocarbons in liquid state. The degree of processing required for Non-associated gas is different from that required for associated gas.
This article will only cover the compression facility for a Non-Associated gas, most of the connected ancillaries will be explained in further sections of this article.
2.1 Natural gas
Natural Gas is a naturally occurring hydrocarbon gas that consists mainly of methane and other higher alkanes. A small percentage of carbon dioxide, hydrogen sulfide, etc. may co-exist with these alkanes which may include ethane, propane, and butane.
Natural Gas is formed when plants and animals (organic materials) buried deep in the earth’s crust are exposed to intense heat and pressure for a long period.
Natural gas is extracted from wells containing only gas or containing liquid (hydrocarbon and water) and gas. Natural gas may be classified either as associated or non-associated depending on the mode of existence.
2.1.1 Associated Gas
This is natural gas existing in hydrocarbon reservoir along with crude oil. The gas may be dissolved in the oil or exist as a free gas cap above the oil. The gas dissolved in the oil can only be extracted from the processing of crude oil.
2.1.2 Non-Associated Gas.
This is also referred to as dry gas or free gas. In some wells, they may co-exist with little quantity of crude oil or condensate.
It should be noted that a large volume of the gas is not dissolved in the liquid but there is usually entrained liquid (Condensate or water) in the gas, therefore, the gas must undergo processing to remove the entrained liquid. The condensate Gas Ratio (CGR) and the Water Gas Ratio (WGR) vary depending on the well composition. Natural gas processing is done by separating all the undesired components from the gas.
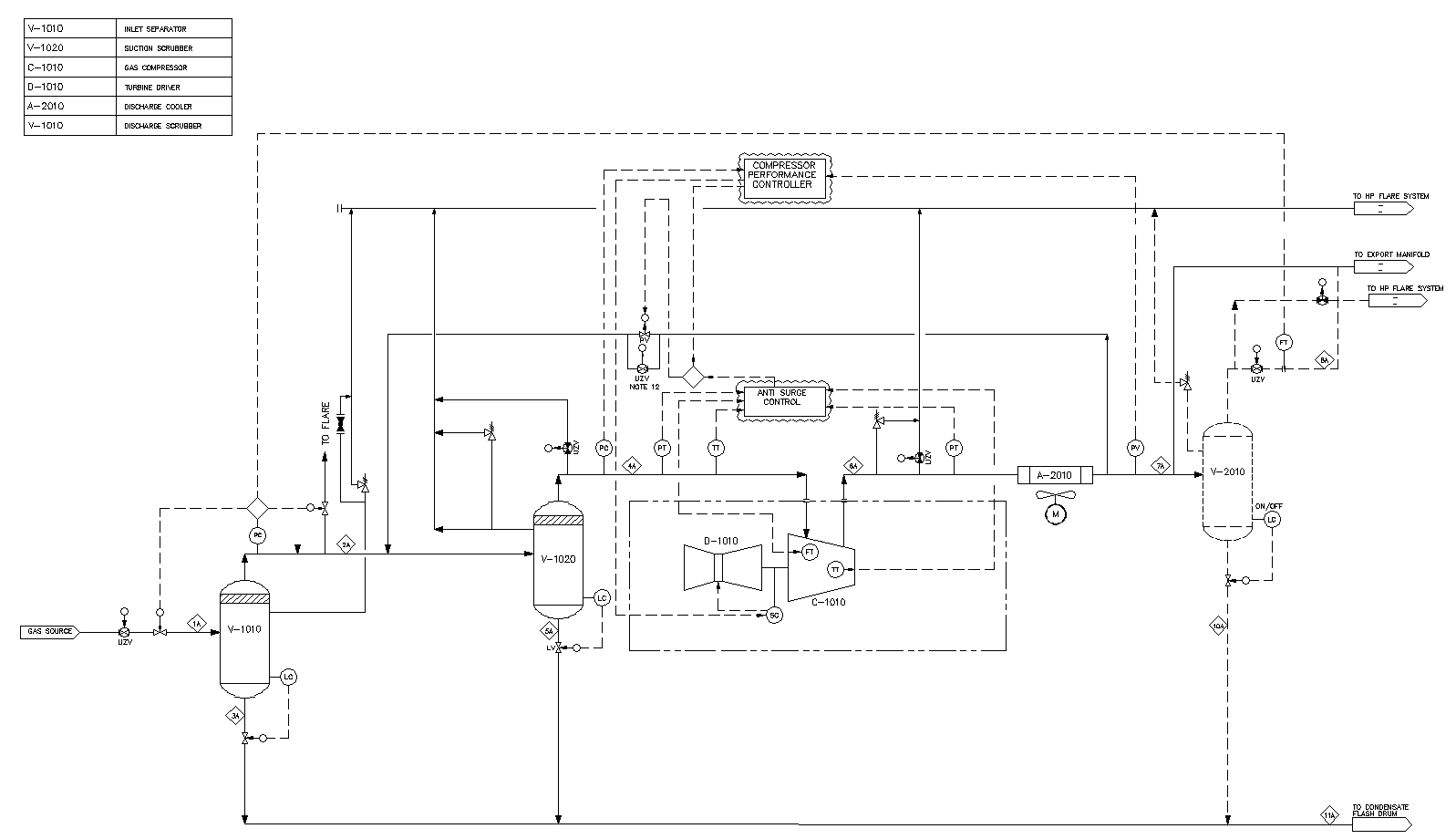
Figure 1: Overview of a Compression Facility
3 Equipment in a Gas Compression Facility
In this section, the equipment installed in a typical gas compression facility will be explained. The components described in this section may not be found in all compression facilities, also the quantity of the equipment may vary depending on the project. The major types of equipment installed in a gas compression facility are inlet separator, compressor suction scrubber, compressor, compressor driver, heat exchanger and a discharge scrubber (optional). There are other equipment’s connected to those listed above which will be explained in this article. The selection of the type and size of equipment is a rigorous task performed by a joint team of engineers made up of process, mechanical, electrical, and instrumentation engineers.
It should be noted that some of the recommendations in this article are company-specific and may not be applicable to other companies, however, they can be used as general guidelines.
3.1 Inlet Separator
Natural gas obtained from well is usually in commingled phase vapour and liquid, therefore, it is necessary to separate the gaseous components from the liquid. To achieve this a separator is used in combination with a scrubber, it should be noted that the initial separation process may be more than one stage depending on the fluid composition and the level of separation desired.
The separator is the primary process equipment in a gas compression train, it separates the components of the fluid (well stream) into liquid and gas component, however, the separated gas may contain entrained gases therefore a scrubber should be installed downstream of the separator.
As defined in section 2.6 of API 12J, A separator is a vessel used in the field to remove well stream liquid(s) from gas components that may be either two-phase which removes the total liquid from the gas or three-phase which also remove free water from the hydrocarbon liquid.
Some of the reasons why separation is necessary are stated below
- Compressors require a liquid-free gas for efficient operation
- Gas measurement device results are inaccurate when there is entrained liquid in the gas
- Gas sales agreement usually requires that the gas contain no liquid
3.1.1 Categories of Separators
Separators are usually classified based on physical appearance in the field. They are categorized as horizontal or vertical separators. Separators may also be classified as two or three-phase separators. A vertical or horizontal vessel can be used as a two or three-phase separator.
3.1.1.1 Horizontal Separators
The horizontal separators are physically identified by their obvious length in the horizontal direction i.e. the axis of the cylinder is horizontal. They are more suitable for processing gas feed with high liquid content; they are more efficient in handling three-phase separation. In addition, they are more efficient in handling foaming crude oil.
Horizontal separators are rarely used in NAG (Non-associated gas) compression facilities.

Figure 2: Horizontal Separators
3.1.1.2 Vertical Separators
Vertical separators are easily identified in the field by the cylindrical axis been vertical. They are mostly used in processing facilities were more gas is produced compared to liquid. Most vertical separators can handle production containing sand and other sediments without fouling. When there is little space available, they have a comparative advantage because they occupy less plot area. Vertical separators are the most applicable in a gas compression train.
3.1.2 Components of a Two-Phase Separator
The components of a two-phase separator are the same as a scrubber except for vessel internals which may differ to obtain higher liquid droplets removal. Below is a short description of the components of a typical pressure vessel (separator)
3.1.2.1 “Vessel body”
“Vessel body” as used in this context is the combination of the vessel shell and the heads.
The vessel body is the pressure-containing element of the separator. Separators are usually cylindrical with varying types of head. Head types used in gas compression trains are usually hemispherical, ellipsoidal or torispherical, however, this is dependent on the pressure, service, or company requirements. As specified in section 5.11 of DEP 31220031 (Unfired Pressure Vessels), SPDC requires that:
Vessel Heads shall be 2:1 ellipsoidal unless specified by or approved by PRINCIPAL.
Hemispherical heads shall not be used except in high pressure services were specified by or approved by the PRINCIPAL
Torispherical heads shall not be used unless specified by or approved by PRINCIPAL
3.1.2.2 Nozzles
The nozzles are the connecting point of all piping.
Inlet Feed Nozzle and Connected Piping
The inlet nozzle is usually the largest amongst all process nozzles connected to the separator, its size should be equal to the inlet feed pipe. It is installed at an appropriate height above the liquid level on the shell of vertical separators, on the top or head of a horizontal vessel.
Some of the criteria for feed inlet nozzle/pipe sizing as specified in SPDC DEP 31.22.05.12-Gen section 3.1.1 are:
Momentum Sizing Criteria
Erosional sizing criteria should also be considered in nozzle/pipe sizing.
Gas Outlet Nozzle and Connected piping
The gas outlet nozzle should be located on the shell above the demisting element in a vertical vessel or on the top head.
For separators with vertical inline vane pack mounted perpendicular to the inlet nozzle, the gas outlet nozzle should have its centreline axis coincide with or above the inlet nozzle.
SPDC requires a vertical vessel gas outlet to be fitted in the middle of the top head.
The momentum criteria for sizing gas outlet nozzle/piping as specified in SPDC DEP 31.22.05.12-Gen section 3.1.1 is:
Gas flow Momentum sizing criteria of gas outlet nozzle/piping is:
Liquid Outlet Nozzle and Connected Piping
Liquid outlet nozzle is installed on the bottom head of vertical vessels, but not in the middle of the head because the drain nozzle is usually installed in the middle of the bottom head.
Some of the criteria for liquid outlet nozzle/pipe sizing as specified in SPDC DEP 31.22.05.12-Gen section 3.1.1 are
- Flow through liquid outlet nozzle for new vessel should not exceed 1m/s (3.3ft/s)
- Liquid outlet nozzle size should not be lesser than 2 DN 50 (NPS 2).
Manways
All Separators (pressure vessels) should have at least one manhole or handhole installed. Manhole size and installation should satisfy vessel design code such as ASME Sec. VIII, PD5500, etc.
Other nozzles
There are other nozzles installed on a separator, they include the drain nozzle usually installed at the middle of the bottom head of vertical pressure vessels or the bottom part of the shell of a horizontal vessel.
Other nozzle connections are for level transmitters, pressure transmitters, flare line etc.
3.1.2.3 Separator Internals
Inlet Distributor
The inlet distributor is used to reduce the momentum of the fluid as it enters the separator. It provide primary separation of the liquid from the gas. There are different types of inlet devices the most common types include: half open pipe, perforated or slotted pipe distributors, v-baffles, deflector plate, vane type inlet device, inlet cyclones.
Separators should be equipped with an inlet distributor to aid gas/liquid disengagement, promote separation, minimize splashing, minimize solids plugging, and prevent erosion of the vessel wall. Vane-type inlet devices and inlet cyclones are preferred to other types of devices. ExxonMobil and SPDC gives preference to vane type inlet devices
Gas Phase Internals (Demisters)
The gas phase internals (demister) is used to separate the entrained liquid from the gas. There are various demisting internals used in separators however, the most common is the wire mesh demister and the vane pack demister
Vortex Breaker
As the liquid in the separator flows out, it will swirl and create a vortex; this will cause some gas to be entrained in the liquid. To mitigate the formation of vortex, a vortex breaker should be installed in the liquid outlet of a separator (pressure vessel)
3.1.3 Gas/Liquid Separation Process
The separation process may be broken down into various sections as described below
3.1.3.1 Primary Separation
The fluid (a mixture of gas and liquid) flows into the separator with a high velocity, the flow is usually turbulent. The primary separation is achieved by impacting the fluid on an inlet distributor device which changes the fluid flow direction. The inlet distributor absorbs the fluid momentum, as the collision continues most of the gas escapes from the well stream (fluid) while the liquid drops down to the separator base.
Note there are other types of inlet device including half open pipe, perforated or slotted pipe distributors, v-baffles, deflector plate, vane type inlet devices, inlet cyclones
3.1.3.2 Gravity Settling
As the gas and entrained liquid enter the large area of the separator, its velocity drops. As the liquid and gas are flowing at a reduced velocity, further separation is achieved in the gravity settling zone. The separator should be sized such that the residence time is sufficient for the gas vapor to escape from the liquid and further into the gravity settling zone. The size of liquid particles exiting the gravity settling zone should not exceed 200 microns because they can overload the coalescing section installed before the gas outlet nozzle. The forces acting on the fluid in the gravity settling zone are the gravity force pulling the droplets downward and the force generated as a result of the forward velocity of the fluid. The velocity force either lifts the droplet upward or horizontally however when both gravitational force and the velocity force balances out the liquid droplet will remain suspended. The velocity at which this occurs is termed the critical velocity. The critical velocity is used for sizing the gravity settling zone.

Figure 3: Separator Showing Different Separation Zones
3.1.3.3 COALESCING
The gas escaping from the gravity settling zone contains entrained liquid. The sizes of the liquid may be up to 200 microns, the entrained liquid can be efficiently removed in the coalescing section.
The coalescing element is installed close to the gas outlet nozzle. The coalescing element can be wire mesh or vane packs, however, wire mesh is mostly used and less expensive. As the gas flows through the wire mesh or vanes, it makes a series of directional changes. The liquid having a greater mass than the gas cannot follow the sudden change in direction. The liquid droplets strike and collect on the wire mesh or vanes. As the liquid droplets coalesce, they fall back into the liquid.

Figure 4: Vane Packs
3.2 Suction Scrubber
The scrubber recovers carryover liquid from the separator. The liquid loading level is much lower compared to that of inlet separators. Scrubbers are two-phase separators, mostly vertical however, there are horizontal scrubbers.
As defined in API 12J section 2.5, Scrubber is a type of separator that has been designed to handle flow streams with unusually high gas-to-liquid ratios, commonly used in conjunction with dehydrators, extraction plants, instruments, or compressors for protection from entrained liquids.
The suction scrubber is installed upstream of the compressor because the entrained liquid in the gas can damage the compressor and render it ineffective.
The suction scrubber has the same physical appearance as the inlet separator; the mode of operation is also the same. The only differences that may exist between the scrubber and the inlet separator are:
- The scrubber is usually smaller than the separator because the liquid loading level is much lower than the separator
- The demisting component might be different; to ensure that liquid droplets that escaped the demisting component of the separator are removed. Scrubber demisting component should remove liquid droplet sizes below 10 microns.

Figure 5: Gas Scrubber
3.3 Compressor
This is the most critical equipment in a compression train; it is the only rotating equipment in the gas compression train. As the gas flows through the separator, scrubber, and piping network, there is a pressure drop. The fluid pressure is mostly insufficient to transport the gas to other processing facilities such as liquefaction facilities, gas export facilities. It is therefore, necessary to increase the gas pressure; this is achieved by installing a compressor to boost the gas pressure
A compressor is a device used to increase the pressure of the gas by reducing the gas volume.
In a typical gas compression train, the compressor may be staged, (single stage, two stage, etc.)
Compressors with more than one stage, after each stage compression, the compressed gas is passed through a heat exchanger and scrubber to reduce the outlet gas temperature and any liquid droplet before the next stage of compression.
Designing the compressor is a task that should be performed by an expert, various process data including suction pressure range, suction temperature range, gas volumes are used in the design of the compressors. The outlet pressure of the compressor must meet the required pressure to transport the gas to its destination.

Figure 6: Single Stage Turbine Driven Compressor
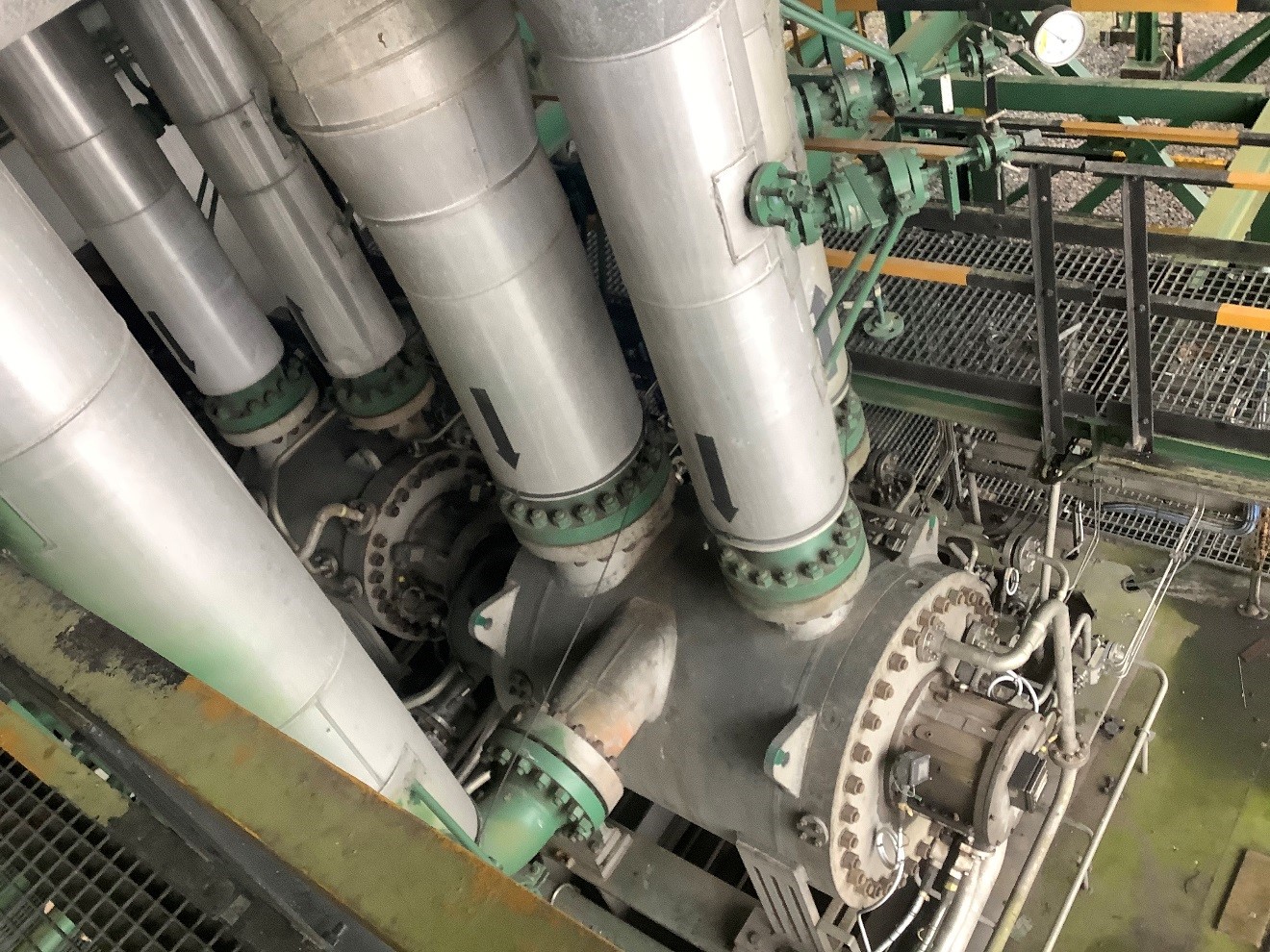
Figure 7: Three-Stage Gas Compressor
3.4 Compressor Driver
Compressors are not self-driven; a prime mover externally drives them. There are various prime movers including
- Diesel, gas-fired engines
- Electrically powered motors
- Gas turbines
Of all the above the gas turbine is the most applicable and most efficient. The turbine is connected to the compressor via a shaft properly aligned. The rotation of the turbines causes the compressor rotation, which performs the gas compression. The turbine utilises natural gas as fuel, the gas s pre-treated to the desired quality as specified by the turbine OEM (Original Equipment Manufacturer). The fuel gas temperature range specified by the OEM must be adhered to. The desired temperature is achieved by installing a Preheaters, superheater, and heat tracing elements depending on the requirements. Heaters will be further explained in subsequent sections.
3.5 Heat Exchanger
The heat exchanger is used to reduce the temperature of the gas to the desired temperature. Compressed gas temperature can sometimes be higher than 100oC, this temperature is too high and must be reduced. Temperature affects pipe material selection as well as piping material class. ASME B16.5 and other codes specify the temperature range for various material classes however; some Companies require lower temperature for the code defined pipe classes. It is necessary to reduce the discharged gas temperature that may eventually lead to a lower pipe class and lesser material cost.
To achieve the temperature reduction a heat exchanger is used. There are different types of heat exchanger including air-cooled heat exchanger, plate type heat exchanger, shell and tube heat exchanger,
Below is a short description of an air-cooled heat exchanger.
3.5.1 Air-Cooled Heat exchanger
This type of heat exchanger is mostly used for heavy-duty gas compression facilities. It is also used where there is water shortage or where there is limited access to clean water.
The air-cooled heat exchanger also referred to as air cooler transfers the heat from the compressed gas flowing through the conducting tubes to the ambient air.
Ambient air is forced to flow vertically across the horizontal tubes, the airflow is generated by the fans installed below or above the tubes.
Air has poor thermal performance therefore to improve its efficiency, the tubes are provided with external fins.
When the fans are installed below the tube section the air cooler is referred to forced draft air-cooled heat exchanger but when the fans are installed above the tube section it is referred to as induced draft heat exchanger.
The most popular is the forced draft some of the advantages and disadvantages of the type of air coolers are:
Advantages of Forced Draft Air Cooled Heat Exchanger
- The fans and upper bearing are easily accessible for maintenance
- Easy accessibility of tubes for maintenance
- It can accommodate higher process inlet temperature
- Lower Fan Horsepower requirements
Disadvantages of Forced Draft Air Cooled Heat Exchanger
- The distribution of air over the tube is lesser compared to induced draft air coolers
- There is a possibility of the hot air recirculating over the bundles; this can result from low discharge velocity.
- The tubes are completely exposed to the atmosphere (rain, sun), this may result in poor process control
Advantages of Induced Draft Air Cooled Heat Exchanger
- The air is better distributed across the bundle
- The possibility of the hot air recirculating over the bundle is low.
- Since the Plenum covers about 60% of the bundle, there is better control of the process.
Disadvantages of Induced Draft Air Cooled Heat Exchanger
- There is a possibility of increased horsepower requirements.
- The fans are less accessible for maintenance and replacement
- To replace the bundles, the plenum must be removed
An induced draft air-cooled heat exchanger is recommended when control of process temperature is desired and hot air recirculation is to be minimised. For other applications that do not require strict control of process temperature and recirculation, force draft air-cooled heat exchanger can be used.

Figure 8: Forced Draft Air Cooled Heat Exchanger
3.6 Discharge Scrubber
The discharge scrubber is similar to the suction scrubber in terms of operation. This static equipment may be installed downstream of the heat exchanger when there is a tendency of liquid droplets formation after the gas has been cooled. It is not mandatory to install this equipment however; process engineering must validate this decision.
The discharge scrubber is usually the smallest of all the “separators”.
3.7 Piping
Depending on the process requirement, fluid composition, facility location, piping material may be of carbon steel, stainless steel or duplex stainless steel. Sometimes the carbon steel pipes used may be lined with corrosion-resistant alloy.
Material selection is critical to prevent catastrophic failure of the piping system. Material selection should take into consideration environmental conditions and the process fluid composition.
When there is a possibility of internal corrosion resulting from the presence of hydrogen sulfide and carbon dioxide in the fluid, stainless steel and duplex stainless pipes are preferred to carbon steel pipes.
When there is a tendency of external corrosion in the form of crevice corrosion, chloride stress corrosion cracking, atmospheric corrosion, the selection of stainless steel, duplex stainless steel piping material in combination with external painting is recommended.
Below is a summary of some major piping connections in a gas compression facility.
3.7.1 Feed Inlet Piping (Inlet Piping to Separator)
Typical gas compression facility with more than one source well, the feed inlet piping originates from the inlet manifold and connects to the inlet nozzle of the separator. The inlet piping is usually the largest of all piping connected to the separator. The inlet nozzle is appropriately located on the pressure vessel shell above the highest liquid level expected in the vessel.
The inlet piping should be sized for two-phase flow (gas-liquid) as determined by the process engineer. The sizing should be performed taking into consideration the pressure drop, erosional velocity, and flow velocity. See section 3.1.2.2 for more details.
3.7.2 Gas Outlet piping
The separator gas outlet piping conveys gas with little entrained liquid from the Separator to the compressor suction scrubber. This piping should be sized for single-phase flow since the liquid entrained in the gas is minimal. The piping is connected to the gas outlet nozzle which should be appropriately located depending on the pressure vessel configuration.
3.7.3 Liquid Outlet Piping (Condensate Piping)
This is the piping connection to the condensate outlet nozzle. In vertical vessels, it may be located on the bottom head but not in the middle of the head. The nozzle connection is usually fitted with a vortex breaker to prevent gas from been entrained in the liquid. The condensate piping conveys the condensate to the storage tank or flash drum.
3.7.4 Scrubber Inlet, Outlet Piping and Condensate Piping
The Scrubber Inlet piping is the discharge from the separator gas outlet. The gas outlet piping of the scrubber may be of the same size as the inlet piping. The piping configuration is the same as described for the separator piping
3.7.5 Compressor Suction Piping
The suction line piping should be connected to the compressor suction nozzle. This piping should be routed taking into consideration piping flexibility. The maximum piping loads should not exceed the allowable compressor nozzle loads as specified by the compressor vendor.
3.7.6 Compressor Discharge Piping
The compressor discharge piping should be connected to the discharge nozzle of the compressor; it should be properly routed with piping flexibility taken into consideration. The discharge temperature is usually very high, therefore the entire compressor discharge piping should be insulated/lagged to protect site personnel from coming into contact with the hot surface. The discharge piping is connected to the heat exchanger where the discharged gas is cooled to a designated temperature.
3.8 Condensate Storage Tank
The condensate storage tank is a very important component of a gas compression facility. The condensate from all the pressure vessels is routed to the storage tank for onward transportation or evacuation. The condensate tank sizing should be done taking into consideration the condensate production rate from the wells.
Condensate storage tanks are mostly made of carbon steel plates
3.9 Relief Valves
A relief valve is a device installed on any vessel (separator, heat exchanger), piping to protect the equipment from excess pressure. Every pressure vessel in a compression train must have at least one relief valve. Relief valves have a set pressure, once the vessel pressure set pressure is reached, the valve automatically open to relieve the excess pressure and automatically close when the pressure is slightly below the set point. The relief line is connected to the pressure relief valve.
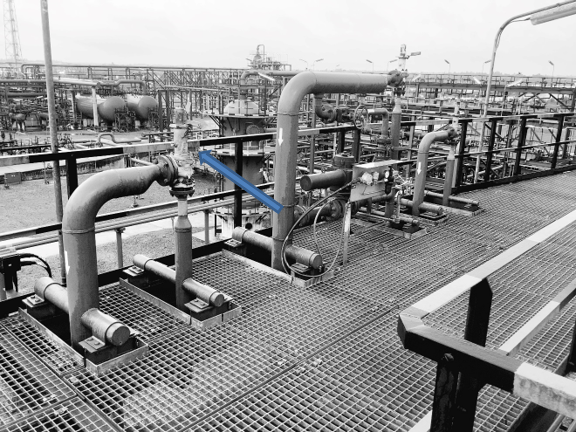
Figure 9: Pressure Relief Valves
3.10 Flare/Vent Lines
The flare lines (High Pressure or Low Pressure) are very critical safety components of a gas compression facility. They are connected to the relief valves on all equipment and piping. They are usually at a higher elevation than all connected equipment and piping i.e. all the relief lines from each equipment are tied to relief header installed at a higher elevation. All pressure vessels and compressors have at least one pressure relief valve that is connected to the flare line. All flare lines are piped to the vent stack or flare stack. Typical flare line piping is mostly made of carbon steel. All the relief lines are piped to the HP Flare line while all low-pressure depressurization is piped to the LP flare line.
3.11 Level Control Valves
A level controlled valve should be installed on the liquid outlet line (Condensate) line. This is the valve that works with the level instrument installed on the pressure vessel. When the Level instrument on the vessel senses a high volume of liquid it triggers the level control valve to open, and automatically close when the level instrument sense low volume of liquid in the vessel.
3.12 Pressure Control Valve
The pressure control valves are safety-critical elements of a gas compression facility. As the name implies they are installed to control the pressure in the system. They also work with the emergency shutdown system to shutdown any section of the system with pressure higher than a particular set point. The pressure control valve can be of globe valve, ball valve or butterfly valve with a controller integrated into the valve.

Figure 10: Pressure Control Valve
3.13 Anti-Surge Control System
The anti-surge control system is a control valve with necessary instrumentation located on a bypass line downstream of the compressor for flow recirculation to the suction line to prevent surge from occurring during compressor operation. The anti-surge system uses a control valve, measurement instruments (pressure, temperature, flow), anti-surge controller to determine the flow at which surge will occur. The bypass line on which the valve is installed should originate from downstream the heat exchanger and tie into the compressor suction scrubber inlet. The anti-surge valve is a fast opening valve with the ability to implement a control function in less than 2 seconds.
3.14 Metering System
It is ideal to measure the quantity of gas entering the compressor and the gas delivered by the compressor, it is therefore, necessary to install a flowmeter upstream and downstream of the compressor. The flowmeter installed downstream of the compressor should be downstream of the discharge scrubber. Orifice flow meters are mostly used for this purpose.
In addition, the quantity of condensate generated by the inlet separator should be measured; this is achieved either by installing a Coriolis meter or any other appropriate meter.

Figure 11: Coriolis Meter
3.15 Compressor Seal and Separation Gas System
The compressor seal and separation gas system is used to prevent the escape of natural gas from the axis of the compressor and deprive the air outside from entering into the compressor. The seal gas pressure should be higher than the maximum pressure the compressor seal will ever experience during operation, a typical compressor seal gas and separation system is divided into three parts:
- Seal and separation gas supply system and vents
- The seal gas housing and other components such as bushing etc.
- Control panel with connecting piping to and from the compressor seals
The seal gas should be clean, dry and compatible with the process gas, while the separation gas is dry inert gas usually nitrogen. In typical compression system, the seal gas may be taken from the compressor discharge header downstream of the discharge scrubber. Filters and dryers may be part of the seal gas control panel to achieve the desired gas quality.
The seal gas vent system is tied to a flare or vent system usually the LP flare header.
Seal gas from the compressed gas header flows into the seal gas control panel where the gas is filtered, dried, and appropriately regulated before it flows into the compressor seal unit.
The separation gas (nitrogen) also flows into the seal gas control unit where it is dried and filtered, the flow is regulated before it enters into the seal gas system.
During project execution the seal gas system is part of the compressor vendor’s package, the engineer’s responsibility is to supply dry clean seal gas to the package.
3.16 Fuel Gas System
The Turbine drives the compressor; the turbine utilizes natural gas as fuel. The fuel gas system is a combination of fuel heaters, gas chromatograph, and interconnecting piping. The Turbine OEM usually specifies the fuel gas requirement.
Below are the components of a fuel gas system.
3.16.1.1 Fuel gas scrubber
The gas scrubber is installed in the fuel gas line to remove entrained liquid. They function the same way as the compressor suction scrubbers.
3.16.1.2 Fuel Gas Coalescer
Gas turbines are very sensitive mechanical equipment especially to solid particles and liquid droplets. It is therefore necessary to install a filter coalescer to remove small particle size solid and entrained liquid. Filters have the capacity to remove particle size up to 1 micron.
Coalescer filters are equipped with internal baffles and coalescing cartridge.
The Filter serves a second stage filtration for the gas to remove solid and entrained liquid.

Figure 12: Fuel Gas Filter Coalescer
3.16.1.3 Fuel Gas Heaters
The heaters are used to preheat the fuel gas to the desired temperature. In some cases, the heating system is a combination of preheaters and superheaters to raise the temperature of the fuel gas to the OEM specified temperature. The heaters may be electrically powered with thyristor control for temperature regulation. For systems with preheaters, the gas from the fuel gas manifold flows into the preheater were the gas temperature is raised to a set temperature of about 40oC. From the preheater, the gas flows through scrubber before entering the filter coalescer were the last filtration occurs. As the gas exit the filter, it enters the superheater, which raises the temperature to the desired temperature of about 60oC. The gas at this set temperature is further transported to the turbine.
Note there are other types of heaters including water bath heaters.

Figure 13: Fuel Gas Superheater
3.16.1.4 Fuel Gas Piping
The fuel gas piping should be made of a material that does not introduce impurities into the gas through corrosion. Most fuel gas piping is made of stainless steel or duplex stainless steel.
Depending on the location of the turbine, the fuel gas piping should be insulated or heat traced to prevent loss of heat as the gas travels to the turbine generator.
3.16.1.5 Gas Chromatograph Unit
The gas chromatograph is used to determine the constituent and quality of the fuel gas and validate that it is in accordance with the required gas composition. The chromatograph unit takes its suction from the fuel gas line and separates the gas into the various components and displays the composition in field or transmit to a control room.
3.17 Instrument Air System
The instrument air is used for valve operation and other pneumatic systems in the facility.
The instrument air is made up of air compressors that take in atmospheric air, filters the air, and sends it into air receiver (Pressure vessel) for storage. The compressor automatically starts when the pressure in the air receiver drops below a set value and shutdown when the pressure reaches a high a set point. The instrument air header originates from the air receiver, it is routed to all location air is needed. Smaller air bottles may be installed close to designated equipment to provide a buffer for the main utility air system.
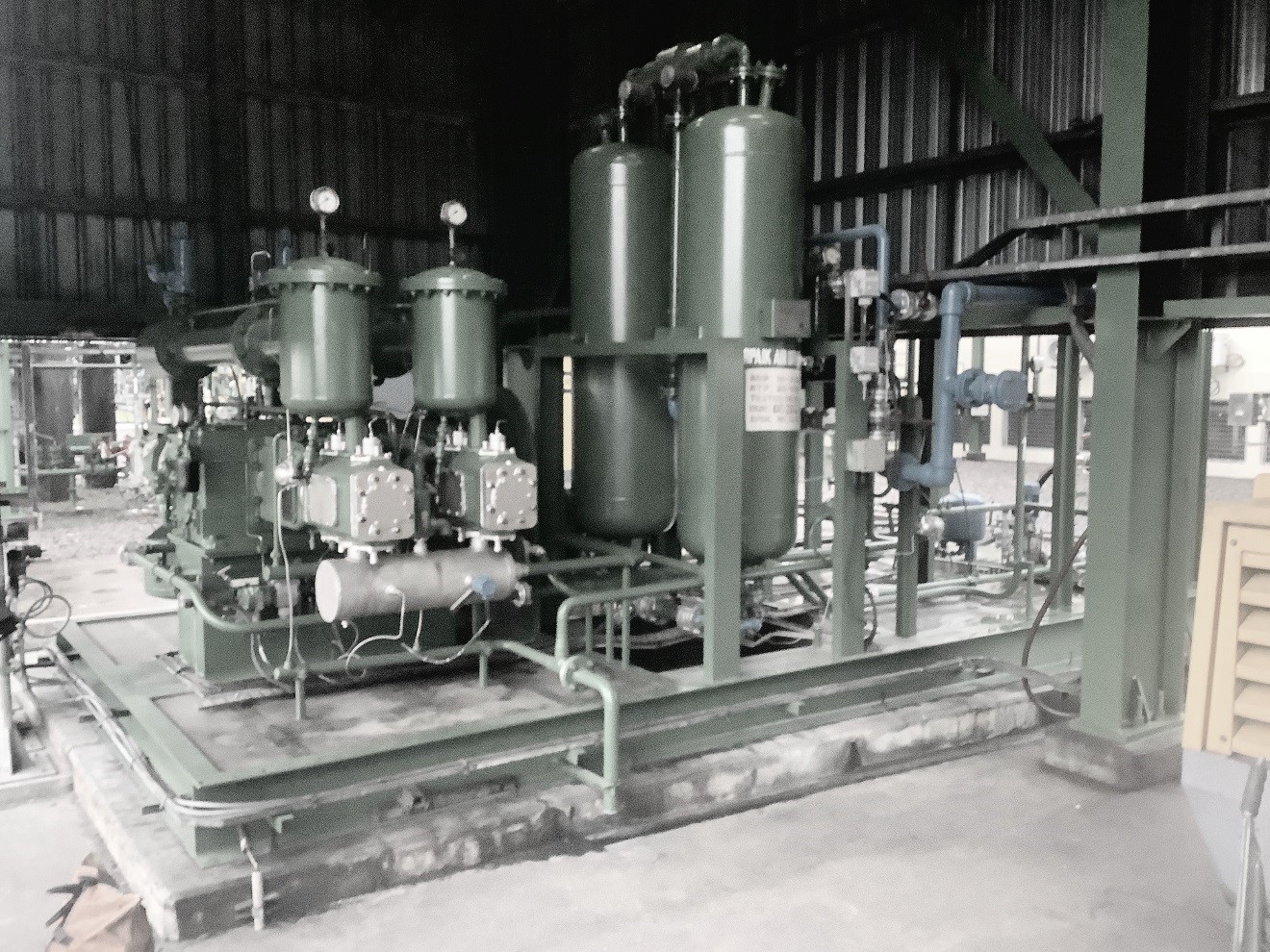
Figure 14: Air Compressor
3.18 Utility Air System
The air compressor generates the utility air; it is usually at a lower pressure compared to the instrument air pressure. The air is sent into a utility air receiver where the air is stored. The utility air is used for cleaning and other utility works in the facility. The utility air piping runs to all equipment especially the compressor.
3.19 Utility Water System
The water is used for washing of equipment and other utility activities. The utility water should be free of pollutants that can cause corrosion to equipment. The clean water is stored in a tank and piped to all equipment installed in the facility. Clean water piping can be made of galvanized steel, PE, or stainless steel.
3.20 Methanol Injection System
The methanol injection package may be installed in some gas compression facilities. It is installed when there is a tendency of hydrate formation in any piping including flare lines. The methanol system is made up of a storage tank/vessel, pump that meters a designated amount of methanol into the piping to prevent hydrate formation.
3.21 Nitrogen Purge System
Nitrogen is an inert gas that can be used to displaced natural gas from piping or equipment. It is used for purging and for the compressor seal gas system.
3.22 Fire Water System
The Firewater system is made up of jockey pumps, main firewater pumps, firewater ring main, firewater monitors and hydrants.
The ring is installed around the entire facility with monitors and hydrants strategically located.
4 References
API 12J: Specification for Oil and Gas Separators
DEP DEP 31.22.00.31-Gen: Unfired pressure vessels
DEP 31.22.05.12-Gen: GAS/LIQUID, LIQUID/LIQUID AND GAS/LIQUID/LIQUID SEPARATORS – TYPE SELECTION AND DESIGN RULES
ASME SEC. VIII. DIV I: Rules for Construction of Pressure Vessels