1 Introduction
Leakage during industrial practices carries the potential to inflict severe environmental harm as well as economic losses. To limit damages, precise leak detection and response mechanism has become a dire need of time for industrial regimes. A Leak Detection and Repair (LDAR) program as a system having multiple procedures, is used by a faculty to identify and fix leaking parts, such as tanks, pumps, valves, compressors connections, and agitators, to reduce the emission of hazardous air pollutants (HAPs) and fugitive volatile organic compounds (VOCs). Its goal is to lessen and completely stop inadvertent liquid and gas emissions. Oil, gas, and chemical processing plants must follow this procedure.
The types of leaks that LDAR detects may be more subtle than the typical domestic pipe leak that most people experience. Gases that are more difficult to visually identify are involved in leaks that contain VOCs and VHAPs. As a result, LDAR employs detection technology that is precise enough to evaluate gas concentrations around components. It is required by law for companies to implement a comprehensive LDAR program. Companies may improve worker safety while lowering product losses by detecting and fixing leaks. These techniques can also aid in environmental conservation due to their ability to reduce the emission of toxic compounds.
2 Why Leak Detection and Repair (LDAR) is needed?
According to the EPA’s research, leakage from industrial equipment such as steam traps, valves, connections, and the like is responsible for the release of VOCs and VHAPs into the atmosphere. Additionally, these kinds of machines produce roughly 9,357 tons of VHAPs and 70,367 tons of VOCs annually, respectively, into the air. The results also show that these gases’ emissions have a significant role in the creation of ozone at ground level, which is a major cause of pollution and respiratory illnesses, particularly in young children and those with asthma. Other alleged issues brought on by the release of these air contaminants include cancer, reproductive issues, and birth deformities. Therefore, to limit these negative impacts, a thorough program for leak detection and repair is urgently needed.
3 What components comprise a Leak Detection and Repair (LDAR) program?
An LDAR program that adheres to best practices will include at least possibly 5 stages. The timing and frequency of each step will change based on the components, national or local regulatory requirements, industrial equipment modifications, and various other reasons. A facility should perform these stages continuously.
The five components of an LDAR system are articulated below.
3.1 Identification of components
All regulated components should be given a special identification number and a location that is known. It is advisable to keep track of replacement components, new equipment additions, and equipment removals in an equipment journal. On the equipment and instrumentation diagrams, ID numbers should be indicated. Trace every component within the building physically and confirm the placement of the desired component. Each component that is subject to the LDAR standards must have a physical tag, according to several states. As soon as new or replacement items of equipment are introduced, be sure to mention them in the equipment journal.
3.2 Definition of Leak
Leaks are defined as measurable concentrations that exceed a common, acceptable threshold depending on the applicable rule, recorded in parts per million (ppm). An acceptable amount may vary depending on the industry and various federal and state laws’ approved standards. Multiple rules could sometimes apply inside the same institution, which creates ambiguities. The EPA suggests defining leakage at a level below the minimum acceptable threshold across all relevant rules to address this issue. Method 21 calls for parts per million (ppm) measurements of VOC emissions from regulated components. Every time the concentration surpasses the relevant regulations, a leak is identified.

Figure 1 Components of LDAR
3.3 Monitoring of Components
EPA Reference Method 21 is the main technique used to monitor elements for the objective of leak detection. A portable detecting device is used in Method 21 to regularly assess emissions. The interval of monitoring is also specified in regulatory standards and may change depending on the sector and certain legislation. The appropriate rule will determine the monitoring frequencies, which are commonly weekly, monthly, quarterly, and annually. The monitoring period for connections might be every two, four, or eight years. The component type, as well as its periodical leak rates, determine the monitoring intervals.
To achieve better outcomes, use an automated (electronic) data recorder for saving time. The whole program should be audited as it will ensure the right direction of the program as well as proper maintenance of the necessary documents. Monitor components more often than allowed by the requirements. Remove any obstacles that can inhibit monitoring at the interface, such as grease on the component interface. The findings of the alternate monitoring technique should still be checked frequently even if a regulation permits the application of alternates to Method 21 monitoring.
3.4 Repairing of Components
Regulations provide a time frame, which may be anything between a few days and several weeks, by which discovered leaks must be fixed. Normally, a leak must be repaired within 5 days of being discovered, and if the first effort becomes unsuccessful, another attempt must be made within 15 days. Other laws specify acceptable repair procedures, such as tightening packing gland nuts or bonnet bolts. Utilizing LDAR tags in asset management systems may assist with equipment reliability assessments, life cycle and predictive maintenance monitoring, and equipment tracking. Efficiency is increased and downtime is decreased by knowing when equipment needs to be repaired or replaced in advance. Operators may simply scan the correct asset tag to automatically add equipment to a maintenance and repair queue rather than manually recording identification numbers and repair requests. In the same way, repair efforts may be recorded more simply without running the risk of obsolete or erroneous data due to human mistakes.
3.5 Record-keeping
Since every regulated component must have extensive information meticulously recorded and maintained with correct information, Leak Detection and Repair rules include high documentation criteria. Data collection is more rapid, less costly, and more accurate when using an asset management system that emphasizes automated identification and data capture. By automating these five components, manpower requirements and overhead expenses are decreased, allowing efficient LDAR administration while lowering complexity and guaranteeing compliance. A facility may significantly lower compliance costs by establishing a complete asset management program that focuses on automated data collection using LDAR tags if operators are still using manual identification and documentation techniques and the facility is subject to LDAR requirements.
The administration of facilities and maintenance is a crucial task that has benefitted immensely from technological advancements, although some maintenance departments haven’t changed much in decades. Innovative technology has had a significant influence on outmoded infrastructure and maintenance management processes where it has been introduced. As a result, certain important patterns have emerged that are expected to change the sector as a whole in the years to come.
The majority of firms no longer use conventional facilities and maintenance management techniques. Paper & pencil approaches pale in contrast to the availability of software programs that interact with current corporate systems in terms of accuracy and data accessibility.
With advanced capabilities and the capacity to carry out a wide range of difficult operations with the aid of mobile applications, mobile devices are more robust and connected in these days.
Nowadays, every mobile can do a variety of tasks, such as scanning barcodes, or simply installing a simple application. Nowadays, practically any goal may be accomplished without ever communicating with another person directly thanks to mobile gadgets.
For improved procedures, routinely conduct internal and external audits of LDAR data to verify compliance. LDAR data should be electronically tracked and archived, along with frequent QA/QC checks. Moreover, maintain records regularly and look for and keep up with new regulatory needs.
4 What Advantages Do LDAR Programs Offer?
When the Leak Detection and Repair regulations were created, the EPA predicted that by adopting a facility LDAR program, petrochemical industries can reduce their leak emissions by up to 60 percent. EPA also predicted that by adopting such a scheme, chemical plants’ VOC emissions could be cut by 56%. Implementing an LDAR program might result in emissions reductions that minimize product losses, improve worker and operator safety, lessen community exposure, lower emissions costs, and assist facilities in avoiding regulatory proceedings.
4.1 Easing Up on the losses of Product
Every time emissions leak from processing machinery, marketable goods are lost in the petrochemical sector. In most cases, lost product equals lost money. Thus, the LDAR minimizes the loss of product.
4.2 Enhancing workers’ safety
For employees and operators who are exposed, many of the substances released by refineries and chemical factories may be hazardous. Reduced occupational exposure to dangerous substances is a direct advantage of lowering emissions from leaky equipment.

Figure 2 increased safety of the workers due to LDAR
4.3 Reducing exposure to the community in the area
The inhabitants of a nearby town may be adversely impacted by persistent contact with harmful emissions due to leaky components, in addition to employees and operators at a plant. Chronic health impacts may arise from prolonged contact with pollutants from the leaky component. Thus, LDAR will save people from such kind of deleterious impacts.
4.4 Possibility of Reducing Emission Penalties and Costs
Various countries and municipal authorities levy yearly charges according to released emissions by a production unit. A facility may be able to reduce the amount of these yearly fees if it has a successful program for decreasing leaky equipment.
5 What Compliance Issues Have Been Identified in Present LDAR Programs?
Numerous regulatory bodies examine submitted documents to evaluate the level of compliance with LDAR programs. Every leak that doesn’t get found and fixed is a missed chance to lower emissions. Many significant variables impair LDAR compliance.
5.1 Not properly identifying all equipment or items in storage
Some leaks can go undetected when a working class is unable to correctly determine every piece of equipment. If the components are not correctly recognized, monitored, and fixed, the number of leaking emissions will continue to surge and will undermine the whole environment.
5.2 Lack of proper monitoring and supervision of components
The number of components claimed to have been monitored may sometimes be a sign of issues with monitoring techniques. For instance, a monitoring record revealed that valves were typically checked once per second, but sometimes two valves would be examined in the same 1-second span. Such behaviors point to inadequate or nonexistent component monitoring.
5.3 The incorrect classification of components as “unsecure” or “hard” to monitor
The reason why a component is labeled as “dangerous to monitor” or challenging to monitor is that the component cannot be properly analyzed due to a safety risk or accessibility problem. All dangerous or complicated equipment needs to be recorded and relevant actions need to be taken to ensure a smooth and safe set of workings.
5.4 Failure to keep a monitoring device up to date
The inability to maintain the equipment properly is a significant barrier to finding leakage. The following are the potential barriers to the instrument’s ability to detect leaks.
- Not utilizing a device that complies with Method 21’s standards.
- Dirty probes for instruments.
- Wrong calibration gases were employed
- The detection apparatus wasn’t calibrated every day.
6 Characteristics of a Model Leak Detection and Repair (LDAR) Program
According to experts, an effective LDAR can minimize leaks thereby providing an impetus to the best industrial practices. The characteristics of a model LDAR program are articulated below.
6.1 A written Leak Detection and Repair Program
The governing requisites and relevant processes are laid up in a documented LDAR program. When the LDAR program is in written form, it effectively outlines the responsibilities of every member of the leak detection and repair staff and lists all the steps that must be taken and the data that must be acquired, ensuring accountability.
6.2 Coaching and Training
Coaching sessions give the practical knowledge needed for implementing the leak detection and repair program. Moreover, training will highlight the specific duties of all individuals.
6.3 Leak Detection and Repair Audits
Effective LDAR program must include both internal and external audits of the facility’s LDAR program. These audits authenticate the utilization of proper monitoring technology, implementation of Method 21 processes, the rectification of leaks, and maintenance of necessary documents.
6.4 Accountability of Contractors
Organizations should have adequate supervision processes to enhance the contractors’ responsibility.
6.5 Definition of Underlying Leak for Valves and Pumps
It may be difficult to correctly detect leaks due to the many leak demarcations related to various equipment. For best practices, it is necessary to run the whole LDAR program with internal definitions of leaks to address the possible issue. These definitions are likely to be less stringent as compared to any authorization as well as the relevant local, state, and federal laws.
6.6 Increased Monitoring
Develop a policy for more regular monitoring of the components that add the most to machinery leak releases to assure that leaks are still found quickly and that earlier discovered leaks are not becoming bigger over time.

Figure 3 efficient monitoring under LDAR
6.7 Repairing Components That Leak
Most standards call for a first effort at repair to be made within the time limit of five days of the leak detection. Moreover, a complete renovation is to be made in not more than 15 days to stop discovered leaks whilst they are fairly tiny. Any item that is not fixed in that amount of time must be added to the “Delay of Repair” list and will need to be fixed during the subsequent shutdown phase.
6.8 Electronically LDAR Data Monitoring and Storage
By using time/date stamps, electronically supervising and recording LDAR information is likely to increase accuracy, and enable efficient quality assurance and quality control. It will also assist assess the effectiveness of monitoring staff.
6.9 Quality assurance or control of Leak Detection and Repair Records
Quality assurance and quality control checks certify the fulfillment of the Method 21 protocols. They also ensure that the staff is properly examining the right equipment.
6.10 Proper calibration of monitoring equipment
Always use the right calibration gas to adjust LDAR monitoring equipment.
6.11 Proper organization and maintenance of Records
One possible sign of a successful LDAR program is organized and accessible records. The LDAR program may be included in the facility’s regular operation and administration, according to well-kept records.
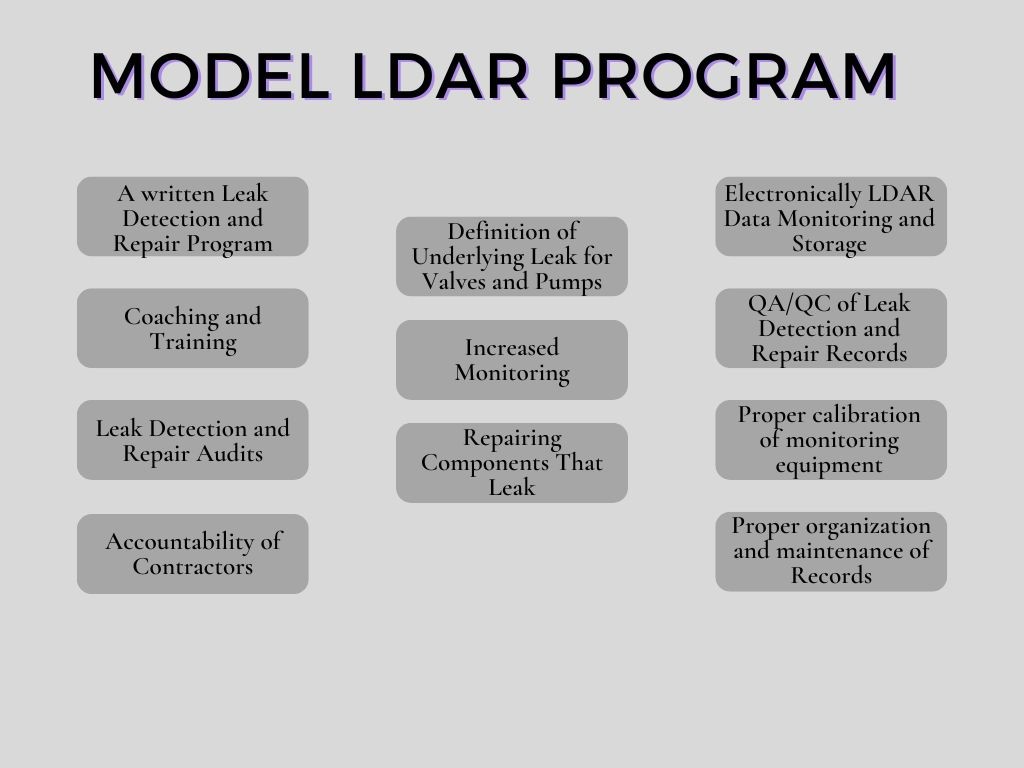
Figure 4 Characteristics of a model LDAR program
7 References
- Fuchs, H. V., and Riehle, R. (1991b). “Ten years of experience with leak detection by acoustic signal analysis.”
Applied Acoustics, 33(1), 1-19. - Griebenow, G., and Mears, M. (1989). “Leak detection implementation: modeling and tuning methods.” Journal
of Energy Resources Technology, ASME, 111, 66-71. - Farmer, E., Kohlrust, R., Myers, G., and Verduzco, G. (1988). “Leak detection tool undergoes field tests.” Oil
and Gas Journal, 86(51), 48-53. - Covas, D., and Romas, H. (1999). “Leakage detection in the single pipeline using pressure wave behavior.” Water
Industry System: modeling and optimization application, Baldock, Hertfordshire, England, 287-299. - Liou, C. P. (1998). “Pipeline leak detection by impulse response extraction.” Journal of Fluids Engineering,
ASME, 120, 833-838. - Corp, Express. “Best Practices Guide: Leak Detection and Repair (LDAR).” Express Corp, 1 Nov. 2019, expresscorp.com/Blogs/best-practices-guide-leak-detection-and-repair-ldar.
- American Water Works Association. (1987). Leaks in the water distribution system: a technical/economic overview,
American Water Works Association, Denver, U.S.