1 Overview of the Article
Pressure Vessels are prominent equipment in a hydrocarbon processing facility. You would find them in a gas processing facility, gas compression facility, crude processing facility, and facilities where gas is used as fuel.
This article is developed to give an overview of two-phase separators. The pressure vessels described in this article are used in typical gas facilities (compression or processing facilities). Though the focus of this article is two-phase separators, three-phase separators will be briefly discussed.
It should be noted that some data stated in this article are as per company requirements and may vary from the requirements of other organisations. Some requirements are drawn from SPDC DEP (Design and Engineering Practice) and writer experience.
2 Introduction
A pressure vessel is a container designed to hold or process fluid (Liquid, gas or both) at a pressure higher than the ambient pressure. A pressure vessel is defined in ASME VIII Div. 1 Section U-1(a) (2) as a container for the containment of pressure, either internal or external. This pressure may be obtained from an external source or by applying heat from a direct or indirect source or any combination.
As previously stated, the pressure vessels discussed in this article are used for hydrocarbon fluids focusing on two-phase separation.
Oil well fluids (Wellstreams) are produced in two commingled phases (liquid and vapour). The liquid component could be free water and other liquid hydrocarbons, while the vapour component could be a mixture of hydrocarbon gasses, nitrogen, carbon dioxide etc.
Ideally, each component of the well stream should be separated, measured and transported separately. The physical separation into individual phase is the activity that is performed in gas or crude processing facilities. The separation may not be achieved in one operation or involve flowing the fluid through several separate equipment.
A typical gas compression facility has a minimum of one separator installed upstream of the gas compressor. The separator removes the liquid component of the stream before the gas flows into the compressor. If the gas entering into the compressor is wet, there will be severe damage to the compressor.
Processed gas used as equipment fuel gas should be free of liquid to prevent damage to the equipment.
Liquid hydrocarbon pumps require a gas-free liquid to operate efficiently. The presence of gas/vapour may eventually damage the pump or result in inefficient flow.
3 Separators
A separator is a pressure vessel designed and constructed to divide or split a commingled liquid-gas stream into the individual phase free of each other. Note that there might be some minimal entrained liquid in the separated gas.
Also, the separated liquid in two-phase separation may contain a minimal amount of free water. The water may be further removed in subsequent separation processes.
3.1 Type of Separators
Separators may be classified based on physical appearance or the separation phases. In some cases, the two classifications listed above may be combined. Each type of separator has specific advantages, and the selection is based on a critical analysis of the vessel performing the separation process. Some of the critical selection criteria include:
- Gas handling capacity
- Liquid removal efficiency
- Liquid handling capacity (Slugs and droplets)
- Fouling tolerance
- Pressure drop
- Available space for installation
3.1.1 Vertical Separators
These vessels are primarily used for low gas-oil ratio fluid separation. Low gas oil Wellstreams mean a larger quantity of oil and less gas. They are suitable for handling fluid with sand and other sediments without fouling compared to horizontal separators. They occupy less plot plan space, which is a significant advantage over horizontal separators when installed on offshore platforms.
For a given capacity of gas, vertical separators are usually larger and more expensive than horizontal separators because the upward flow of gas opposes the falling liquid from the inlet rather than travelling perpendicular as in horizontal separators.
Two-phase separators such as inlet separators and scrubbers are primarily vertical.

Figure 1: Vertical Separators
3.1.1.1 Vertical Two-Phase Separators
Vertical two-phase separators are more popular than vertical three-phase separators. They are very popular in gas compression facilities. The inlet stream flows into the vessel through an inlet nozzle located halfway to the vessel’s height, depending on the maximum liquid level. The inlet stream strikes a deflector installed over the nozzle; this induces separation by causing most liquid to fall to the bottom while the gas flows upward. Some other types of inlet devices will be briefly discussed in this article. Other gases that could not escape as the stream hits the deflector will escape from the liquid surface. The escaping gas flows through a mist extractor located before the outlet nozzle. The mist extractor further removes entrained liquid in the gas by collecting the liquid into larger sizes that will fall to the vessel’s liquid.

Figure 2: Cut Section of a Typical Vertical Two-Phase Separator
3.1.1.2 Vertical Three-Phase Separators
These vessels are not very popular. The significant difference between the two-phase and the three-phase vessel is the vessel’s internals. The internals may vary amongst vessels. The three fluid mostly separated are oil/condensate, water and gas. Because the two liquid has a different density, their separation can be easily achieved. The lighter liquid will be above. A separator should not be used to separate oil and water that exists as an emulsion. Emulsions separation require other forms of separation and treatment.
In three-phase separators, the fluid enters the vessels as described in vertical two-phase separators. After striking the inlet device, most gas will escape and travel upward to the outlet nozzle while the liquid will fall downward. The falling liquid may drop on an isolation baffle and flow through a downcomer into the lower section of the vessel. The liquid mixture is allowed a quieting period to allow for separation by density. The two liquids are released separately by level controls installed on the vessel, one for water and the other for oil/condensate.
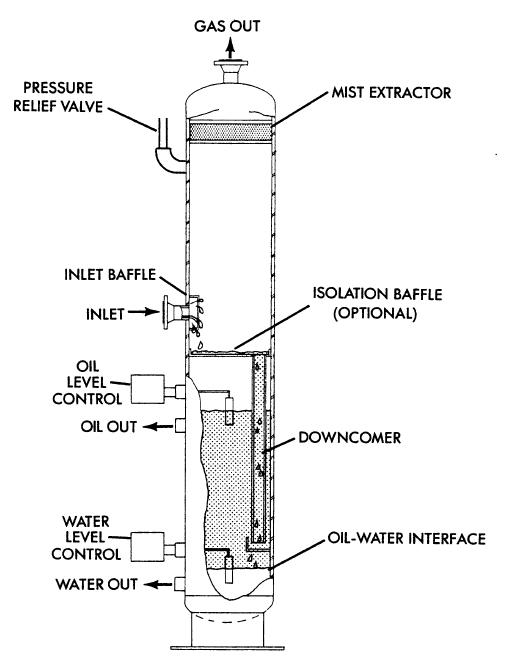
Figure 3: Cut Section of a Typical Vertical Three Phase Separator
3.1.1.3 Scrubbers
Though scrubbers are separators, the word scrubber describes a vessel that removes entrained liquid from gas while a separator splits the fluid/stream (commingled liquid and gas) into liquid and gas. Scrubbers are used where there’s a high gas-oil ratio; they are usually vertical but can be horizontal.
Scrubbers are two-phase separators designed to remove entrained liquid from the gas. The liquid loading level is lower compared to separators. They are usually installed upstream of gas compressors, upstream of vent or flare etc. They are considerably smaller than the inlet separator when installed in a gas compression system because the liquid content removed from the gas is usually minimal. There are other types of scrubbers, including filter separator, cyclone mist extractor etc.
3.1.2 Horizontal Separators
These separators are primarily suitable for three-phase separation. They occupy a larger plot plan compared to two-phase separators. They are not popular in gas compression facilities compared to crude oil processing facilities. These separators have a larger gas-liquid interface area; therefore, they are very suitable for handling foaming hydrocarbon liquids (crude oil/condensate)

Figure 4: Horizontal Separator
3.1.2.1 Horizontal Two-Phase Separators
The horizontal two-phase separator operates like a vertical two-phase separator. The inlet nozzle may be located on the top of the shell or the head. The outlet nozzle should be located on the top of the shell or the opposite head to the inlet nozzle, depending on the design configuration. The separation process is similar to the vertical two-phase separator already explained. Horizontal two-phase separators are mainly used when emulsions are present in the fluid. The emulsion is released through a nozzle at the bottom of the vessel and flows to other treatment equipment for further separation.
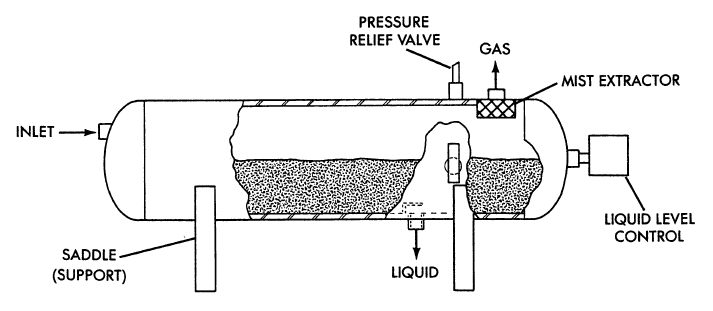
Figure 5: Cut Section of a Typical Horizontal Two-Phase Separator
3.1.2.2 Horizontal Three-phase Separator
The significant difference between the horizontal two-phase and three-phase separator is the internals used to separate the liquid. The design may vary depending on the manufacturer. Typical three-phase separators have weir (dams) and buckets that are used to control the liquid level. Below is a typical section of a horizontal three-phase separator.

Figure 6: Cut Section of a Horizontal Three-Phase Separator
4 Componenta of Two-phase Separators
4.1 Vessel Externals
The term vessel external as used describes the part of the vessel that is seen from outside. The subsections below give a brief overview of the externals.
4.1.1 Vessel Body
As used in this context, the vessel body is the pressure-retaining component of the pressure vessel. It is composed of the head and the shell with the connecting nozzles. The vessel body should be design to withstand the maximum pressure the vessel will ever be subjected to. Usually, the design pressure is higher than the maximum operating pressure of the vessel.
4.1.2 Vessel Support
In most cases, pressure vessels are supported, i.e. not resting on the ground. Therefore adequately rated support shall be welded to the vessel to carry the operating load.
Note not all vessels have supports; typical examples of vessels without supports are buried and mounded pressure vessels used to store LPG or other products.
Below are the types of pressure vessel supports
4.1.2.1 Skirt
Skirt support is the most common support for large vertical cylindrical vessels. Large vertical cylindrical vessels are supported on skirts. The skirt shall be continuously welded to the shell of the vessel. All skirts should be provided with vent holes. It is recommended not to install flanges inside the skirt area, most especially for cryogenic cases. The nozzle connected to the skirt area should be routed outside with a combination of pipe and elbows.

Figure 7: Vessel on Skirt Support
4.1.2.2 Lug Support
Lug supports are very rare and should not be used for cryogenic services. They are mainly used for small diameter vertical vessels not supported from grade. In typical offshore application, they are supported on the deck while they penetrate through the deck.
The lugs should be attached to a pad fully welded to the vessel. The pad material should be of the same group as the vessel.

Figure 8: Lug Support on a Vertical Pig Launcher Penetrating Offshore Platform Deck
4.1.2.3 Leg Support
Spherical vessels shall use only leg supports. Also, they are used for small diameter cylindrical vertical vessels. A Vessel with a diameter lesser than 1500mm may be supported on legs. Depending on the vessel diameter, three or four legs may be used, but this also depends on the organisation.
The legs support should not be welded directly and should be welded to a pad of the same material group as the pressure vessel.

Figure 9: Vessel Supported on Legs
4.1.2.4 Saddle Support
Horizontal vessels are supported on saddles. The saddle should be appropriately designed to carry the operating weight of the vessel. The saddle support should have a base plate, wear plate, top flange, web and stiffeners to provide the required strength to support the vessel. Usually, there is a standard Saddle Support Size depending on the weight of the vessel. This should be validated with analysis.

Figure 10: Vessel Supported on Saddles
4.1.3 Lifting Trunnions and Lifting Lugs
Lifting Lugs/Trunnions are attachments to the vessel utilised during the lifting of the vessel.
Vertical vessels are provided with two lifting lugs or trunnions. When installed on horizontal vessels, two or four lifting lugs may be provided on a horizontal vessel. Lifting lugs and trunnion should be welded to a pad not directly on the pressure vessel.
A weight or load factor of safety of about 1.35 to 2 is applied to the lifting device design,
Also, note that vertical vessels with a weight of about 20 tons should have a tailing lug installed perpendicular to the axis of the lifting lugs/trunnions.

Figure 11: Lifting Lugs
4.1.4 Nozzles
Depending on the complexity of the pressure vessel, the number of nozzles may be over six (6).
Nozzles may be as per ASME 16.5, 16.47, depending on the design code.
Below are some of the nozzles
4.1.4.1 Feed Inlet Nozzle
The fluid enters the separator through the inlet nozzle. The feed inlet nozzle shall be located on the vessel shell for vertical vessels at an appropriate distance from the maximum liquid level. The feed inlet should either be located on top or in the vessel’s head at an appropriate distance above the maximum liquid level for horizontal vessels. Other requirements for feed inlet nozzle may vary across organisations. The internal diameter of the nozzle should be equal to the internal diameter of the upstream piping. As per SPDC DEP, devices that generate sudden pressure drop such as elbows, reducers, flowmeters, valves should be located more than 10D (10 pipe diameter) from the inlet nozzle. If a valve is to be located at a distance less than 10D, the valve should be full bore. For a vessel with little liquid in the inlet stream, such as scrubbers, the 10D distance may be reduced to 3D.
4.1.4.2 Gas Outlet nozzle
The gas outlet nozzle is the exit point for the separated gas. The location of the nozzle may vary depending on the location of the mist extractor in the vessel. Some organisations require that the gas outlet nozzle for a vertical separator be fitted in the middle of the top head. In contrast, some organisations allow the outlet nozzle to be fitted on the vessel shell. The gas outlet nozzle should not be smaller than the connecting gas outlet piping. The piping connection to the gas outlet nozzle should have the same diameter as the nozzle for a distance of 2D (2 x Pipe Diameter).
4.1.4.3 Liquid Outlet Nozzles (Including Drain Nozzle)
For vertical vessels having a drain connection, the liquid outlet nozzle should be located on the bottom head of the vessel. The drain nozzle should be fitted at the centre of the bottom head, while the liquid outlet nozzle should be located on the bottom head at an appropriate distance from the drain nozzle. For horizontal vessel, the liquid outlet nozzle should be located on the shell at the bottom. Drain nozzles on horizontal vessels may be more than one to ensure the vessel is entirely drained. The distance between the drain nozzles should be carefully analysed. For new vessels, SPDC requires that the liquid outlet nozzle should not be lesser than 2”, satisfying a maximum flow velocity of 1m/s (3.3ft/s). Piping connecting to the liquid outlet nozzle should have the same diameter as the nozzle for a minimum distance of 2D (2 x Pipe Diameter) before valves, reducers, and bends should be installed.
4.1.4.4 Manhole/Handhole
The Manhole is the access to the inside of a pressure vessel. Recommended minimum Manhole size for a vertical vessel is 24″; however, sizes lesser than 24″ may be used for small diameter vessels. Manhole installed on top of a horizontal vessel may be of size up to 30″ to accommodate ladders that may be required during maintenance. Also, a handhole may be installed in place of a manhole for tiny diameter vessels. Handhole size should be 6″.
Manholes and handholes should be covered with an appropriately rated blind flange.
12” size and above manholes cover should be provided with davits. The direction of opening of the flange/davit assembly should be such that it does not obstruct access.
4.1.4.5 Instrument Connection Nozzles
Various instruments nozzles should be located on the vessel. Instruments are connected to the nozzles via a mating flange. Instrument nozzles should be a minimum 2″ size and should not be located where components in the feed stream will clog them.
A level instrument nozzle should be located on the vessel’s shell within the liquid section on vertical separators. Depending on the level instrument configuration, there might be a minimum of two nozzles for the level gauge or transmitters.
There should be nozzle connection for pressure instruments such as pressure gauges and transmitters. A pressure instrument nozzle should be located on the head or above the demisting device for vertical vessels. Also, there might be provision for two nozzles across the mist extractor used for differential pressure measurement.
4.1.4.6 Relief Connection Nozzle
All pressure vessels should be equipped with a relief device. This nozzle should be located on the upper part of the vessel shell or the head. However, the relief valve should be installed at an elevation higher than the vessel.
4.2 Vessels Internals
Two-phase separators internals vary. Some organisations have developed proprietary internals to boost the fluid separation process. Below are some of the internals.
4.2.1 Vessel Inlet Devices
There are various inlet devices. As the inlet stream hit the inlet device, separation is initiated by reducing the inlet fluid momentum.
4.2.1.1 Deflector Plate
The deflector plate is made by welding plate material together over the inlet nozzle. A deflector plate is used for non-critical vessels. The momentum reduction efficiency is average, used when the maximum momentum is around 1500Pa. The cost of this inlet device is low compared to other inlet devices.
4.2.1.2 Half Open pipe
A half-open pipe is used when the maximum inlet fluid momentum is about 3000Pa. They are better than the deflector plate.
4.2.1.3 Vane Type Inlet Devices
These are special and more efficient type inlet device. Vane type inlet devices are used for bulk and critical separation process. There are various propriety versions, including Schoepentoeter developed by Sulzer Chemtech and Shell, ZP-Vane Type Inlet Device developed by Zeta PDM. They can handle very high momentum fluid and initiate separation with high efficiency. These type of devices are costly compared to those previously discussed.
4.2.1.4 Cyclonic Inlet Device
Like the vane-type inlet devices, the Cyclonic inlet device is efficient. They are mainly used for bulk and critical separation process. Various proprietary versions exist of this equipment, such as VORSOMAX® Cyclonic Inlet Device, Jonell Systems ALTA-Cyclone.
4.2.2 Vessel Demisting Devices
Demisting devices remove the carryover liquid in the gas. They are installed close to the gas outlet nozzle. There are various demisting devices, including Wiremesh demister, vane pack demister, demisting cyclones etc.
Vertical wire mesh demister should be used in vertical separators, while the horizontal wire mesh demister should be used for horizontal vessels.
4.2.3 Vortex Breaker
During the flow of liquid from the liquid outlet nozzle, the fluid rotates, which can eventually result in gas been transported with the liquid. To prevent this occurrence, a vortex breaker is installed on the liquid outlet nozzle. Note this may not be applicable to drain nozzles.
5 References
ASME Section VIII Div. 1: Rules for Construction of Pressure Vessels
DEP 31.22.05.12-Gen: Gas/Liquid, Liquid/Liquid and Gas/Liquid/Liquid Separators – Type Selection and Design Rules
DEP 31.22.00.31-Gen: Unfired Pressure Vessels