1 Overview of the Article
This article covers onshore pipeline wall thickness calculation – based on the ASME B31.8 standard.
Stress calculation will also be briefly discussed, and a sample calculation for wall thickness analysis is presented in this article.
Other codes and standards utilised for pipeline design (onshore and offshore) will be briefly explained before being narrowed to ASME B31.8.
This article covers pipelines made of carbon steel materials with an emphasis on API 5L line pipe material.
Note that though the word design is used to describe the codes and standards referenced, these codes have broader application beyond pipeline design.

Figure 1: Onshore Pipeline Undergoing Construction
2 Introduction
Pipelines convey fluid from one point to another. The fluid could be in the gaseous state, liquid state, or multiphase fluid.
Single-phase flow pipelines are those conveying product existing predominantly in either the liquid or gaseous state. These fluids include processed hydrocarbon gas (methane, ethane, etc.), refined liquid hydrocarbon products (ATK, DPK, PMS, and AGO) Liquefied Petroleum Gas (Butane, Propane), etc.
Multi-phase flow is mostly encountered when crude or natural gas is extracted and transported for processing.
There are designated codes and standards that govern the design, construction, testing, and operation of pipeline transporting categories of fluid related to the fluid state. Though some codes are specific to a category of fluid, some cover all the categories.
This article’s focus is on the ASME B31.8 standard with a focus on the wall thickness calculation. Note that the ultimate governing regulations are the local standards and regulations; other codes can only be applied to the local regulations.
2.1 Pipeline Design Codes and Standards and Local Regulations
In this section, I will briefly describe some of the codes and standards used for pipeline design.
Though there are numerous codes and standards, the local regulations should strictly adhere to. In the absence of local regulations, the COMPANY must determine the codes used for pipeline design. Some of the codes described here do not holistically capture the wall thickness analysis. However, they have significant application in the determination of pipeline wall thickness.
PD 8010 (Code of Practice for Pipelines)
This is a British code. It was formerly BS 8010. It is divided into two (2) parts as described below.
Part 1 – Steel Pipelines on Land. This part of the code covers only onshore pipelines. As stated in section 1 of the code; this part of PD 8010 gives recommendations for and guidance on the design, selection, specification, and use of materials, routing, land acquisition, construction, installation, testing, operation, maintenance, and abandonment of land pipeline systems constructed from steel.
This part of PD 8010 applies to pipelines that may be used to carry oil, gas, and other hazardous substances by nature of being explosive, flammable, toxic, reactive, or able to cause harm persons or the environment.
Part 2: This part of the code covers subsea pipelines. As stated in section 1 of the code; this PD 8010 recommends guidance on the design, use of materials, construction, installation, testing, commissioning, and abandonment of carbon steel subsea pipelines in offshore, nearshore and landfall environments. Guidance on the use of flexible composite pipelines is also given.
It is not intended to replace or duplicate hydraulic, mechanical, or structural design manuals. This part of PD 8010 applies to subsea pipelines intended to convey hydrocarbon liquids, hydrocarbon gases, and other gases, liquids and gases in two-phase flow, fluid-based slurries, and water.
ISO 13623 (Petroleum and Natural Gas Industries — Pipeline Transportation Systems)
The scope coverage of this standard is defined in section 1, as stated below.
This International Standard specifies requirements and gives recommendations for the design, materials, construction, testing, operation, maintenance, and abandonment of pipeline systems used for transportation in the petroleum and natural gas industries. It applies to pipeline systems on land and offshore, connecting wells, production plants, process plants, refineries, and storage facilities, including any section of a pipeline constructed within the boundaries of such facilities for its connection.
This is a standard developed by the International Organisation for Standardisation. It applies to rigid metallic pipelines such as steel pipelines and does not cover flexible materials and glass-reinforced plastics.
CSA Z662 (Oil and Gas Pipeline Systems)
This is a Canadian standard that covers the design, construction, operation, and maintenance of oil and gas industry pipeline systems that convey
- Liquid hydrocarbons, including crude oil, multiphase fluids, condensate, liquid petroleum products.
- Natural gas liquids, and liquefied petroleum gas;
- Oilfield water
- Oilfield steam
- Carbon dioxide used in oilfield enhanced recovery schemes;
- Gas
For other details of the extent of coverage of this standard, refer to section 1 of the standard.
DPR P-1P (Guidelines and Procedures for the Design, Construction, Operation and Maintenance of Oil and Gas Pipeline Systems in Nigeria- 2007)
This is a local guideline developed by the Department of Petroleum Resources of Nigeria. The guideline applies to all pipeline systems employed to transport hydrocarbon fluid or fluids associated with petroleum exploitation, production, refinery, and product distribution.
ASME B31.4 (Pipeline Transportation Systems for Liquids and Slurries)
This pipeline Code is one of the codes published by The American Society of Mechanical
Engineers for Pressure Piping, ASME B31. The scope of this code is documented in section 400.1 below is an extract of the scope:
This code prescribes requirements for the design, materials, construction, assembly, inspection, testing, operation, and maintenance of piping transporting liquids between production facilities, tank farms, natural gas processing plants, refineries, pump stations, ammonia plants, terminals (marine, rail, and truck), and other delivery and receiving points.
This code also prescribes requirements for the design, materials, construction, assembly inspection, testing, operation, and maintenance of piping transporting aqueous slurries of non-hazardous materials such as coal, mineral ores, concentrates, and other solid materials, between a slurry processing plant or terminal and a receiving plant or terminal.
This code covers both onshore and offshore pipelines.
ASME B31.8 (Gas Transmission and Distribution Piping Systems)
This is another code for pressure piping developed and published by the American Society of Mechanical Engineers. Its scope is described in section 802. An excerpt from the scope section is below:
This code covers the design, fabrication, installation, inspection, and testing of pipeline facilities used to transport gas. This code also covers the safety aspects of the operation and maintenance of those facilities.
This code covers both onshore and offshore pipelines.
3 General Terms in Pipeline Design
Some general terms used in the design of onshore gas pipelines are explained below.
Some of the explanations are drawn from codes and standards, including API 5L, ASME B31.8 ASTM A106, ASTM A53, and ISO 13623. For more details, refer to the applicable code.
3.1 Pipe
A pipe is a hollow section usually but not necessarily cylindrical for transporting fluid (gas, liquid, slurries etc.). The pipe described in this article is those of a cylindrical hollow section made of carbon steel.
Carbon steel pipes are categorised according to the manufacturing process.
Below are some of the types of carbon steel pipes as per the requirement of ASME B31.8
3.1.1 Seamless Pipes (SMLS Pipe)
As defined in section 4.56 of API 5L, Seamless pipes are pipes without a welded seam, produced by a hot-forming process, followed by cold sizing or cold finishing to produce the desired shape, dimensions and properties.
3.1.2 Welded Pipes
These pipes are made by bending and welding metal sheets or plates into a cylindrical shape to form a pipe.
There are different type of welded pipes; these pipes are defined in API 5L and ASME codes. Note each type of welded pipes has a weld joint factor that is utilised in wall thickness calculation. Below are some types of welded pipes defined in API ASME B1.8.
3.1.2.1 Continuous Welded Pipes
These types of pipes are defined in section 804.7.3 of ASME B31.8 as stated below.
This is a form of Furnace-welded pipe produced in continuous lengths from coiled skelp and subsequently cut into individual lengths. The pipe’s longitudinal butt joint is forged-welded by the mechanical pressure developed in rolling the hot-formed skelp through a set of round pass welding rolls. Typical specifications are API 5L and ASTM A53.
3.1.2.2 Electric Resistance Welded Pipes (ERW Pipes)
These are pipes produced in individual lengths or continuous lengths from coiled skelp and is subsequently cut into individual lengths. The resulting lengths have a longitudinal butt joint wherein coalescence is produced by heat obtained from resistance of the pipe to the flow of electric current in a circuit of which the pipe is a part, and by applying pressure. Typical specifications are API 5L, ASTM A53, ASTM A135, and ASTM A984.
3.1.2.3 Electric Fusion-welded Pipe
These are pipes having a longitudinal butt joint wherein coalescence is produced in the preformed tube by manual or automatic electric-arc welding. The weld may be single or double and may be made with or without filler metal. Typical specifications of electric fusion welded pipes are ASTM A139 and ASTM A134 that permit single or double weld with or without filler metal. Additional typical specifications are ASTM A672 and ASTM A671, requiring both inside and outside welds and filler metal.
3.1.2.4 Electric-Flash-Welded Pipe
As defined in section 804.7.3 (d);
These pipes have a longitudinal butt joint, wherein coalescence is produced simultaneously over the entire area of abutting surfaces by the heat obtained from resistance to the flow of electric current between the two surfaces, and by the application of pressure after heating is substantially completed. Flashing and upsetting are accompanied by expulsion of metal from the joint. A typical specification is API 5L.
3.1.2.5 Spiral-Welded Pipes
These pipes are made by electric fusion welding process with either a butt joint, a lap joint, or a lock-seam joint. Typical specifications are ASTM A134, ASTM A139 (butt joint), API 5L, and ASTM A211 (butt joint, lap joint, or lock-seam joint)
3.1.2.6 Submerged Arc Welded
These pipes have one or two longitudinal weld/seams or one helical weld seam produced by submerged-arc welding.
Submerged-arc welding as defined in section 4.59 of API 5L is Submerged arc welding (SAW) is a process in which the joining of metals is produced by heating with an arc or arcs between a bare metal electrode or electrodes and the work. A blanket of granular fusible material shields the arc on the work. Pressure is not used. Note, contact pressure is not used, and part or all of the filler metal is obtained from the electrodes.
Submerged-arc longitudinal welded pipes may have one or two seams while submerged-arc helical welded pipes usually have one seam.
3.2 Weld Joint Factor
The weld joint factor is a reduction factor applied to the strength of the pipe.
This factor is used to accounts for how closely a welded pipe joint approximates the quality of the seamless parent material.
In simple terms, the weld joint factor is the ratio of a pipe welded joint’s strength to the base metal’s strength.
The weld joint factor depends on the manufacturing or welding process of the pipe.
Seamless pipes have a weld joint factor of one (1) because these pipes have no weld joint, however, depending on the welding process employed in the manufacturing of welded pipes, the factor may be lesser than one (1)
Below are the weld joint factors for different types of pipes, the table is an extract from ASME B31.4 Table 403.2.1-1 and ASME B31.8 Table 841.1.7-1
3.3 Pipeline Nominal Wall Thickness
This is the wall thickness computed using an applicable equation such as those stated in paragraph 841.1.1 of ASME B31.8 or any other applicable code. The nominal wall thickness computed may be used to order the pipe with or without allowance to compensate for under thickness.
3.4 Restrained Pipeline
These are pipelines that soil or supports prevents it from displacing in the axial direction at bends.
Restrained pipelines include:
- Straight sections of buried pipelines
- Bends and adjacent pipeline buried in stiff or consolidate the soil
- Any section of an aboveground pipeline on rigid supports
3.5 Unrestrained pipeline
These are pipelines that are free to move/displace axially or flex at bends
Unrestrained pipelines include
- Pipelines buried in unconsolidated soil
- Aboveground pipelines configured to accommodate thermal movement or anchor movement through flexibility
- Pipes subject to endcap pressure force
3.6 Design Pressure
Design pressure is the pressure used in calculations or analysis of all pressure design component.
Generally, the pipeline will never experience the design pressure.
3.7 Maximum Operating Pressure (MOP)
This is the highest maximum pressure the pipeline is operated during the normal operating cycle.
3.8 Maximum Allowable Operating Pressure (MAOP)
This is the maximum pressure a pipeline may be operated per the code the pipeline is designed and operated.
3.9 Pipeline Right of Way (ROW)
The right of way is a strip of land which the pipeline and other facilities are constructed.
As defined in ISO 13623, the right of way is a corridor of land within which the pipeline operator has the right to conduct activities per the agreement with the landowner. The right of way agreement gives the right to pass over the third party owned properties to the pipeline operator (owner). The width of the right of way varies depending on the pipeline construction methodology, the number of pipelines to be installed within the right of way, pipeline maintenance requirements etc.
3.10 Pipeline location class
The pipeline location class describes the population density or building occupancy along the pipeline right of way.
As defined in ASME B31.8 section 805.1.1; the location class is a geographical area along the pipeline classified according to the number and proximity of buildings intended for human occupancy and other characteristics that are considered when prescribing design factors for construction, operating pressures, and methods of testing pipelines and mains located in the area and applying specific operating and maintenance requirements.
In setting the location class, consideration should be given to future development along the pipeline route. A location class 2 can become a location class 3 in a few years.
For a full explanation of location class refer to section 840.2.1 of ASME B31.8, however below is a summary of the location classes.
3.10.1 Location Class 1
This is used to depict areas with sparse populations such as wasteland, mountains, deserts, farmlands. As defined in section 840.2.2 (a) location, class 1 is a 1-mile (1.6-km) section that has ten (10) or fewer buildings intended for human occupancy. Location class 1 has two divisions:
Class 1, Division 1: This is a location where the design factor used for pipeline design is greater than 0.72 but lesser than or equal to 0.8. Also, the pipe must have been hydrostatically tested to 1.25 x MOP (Maximum operating pressure).
Class 1, Division 2: This is a location where the design factor used for pipeline design is lesser than or equal to 0.72. The pipes must have been tested to 1.1 x MOP
3.10.2 Location Class 2
This is a location where 1-mile (1.6km) section has more than ten buildings but fewer than 46 building intended for human occupancy. Location class 2 depicts areas with a population density between class 1 and class 3.
3.10.3 Location Class 3
This is a 1-mile (1.6km) section with 46 buildings or more than 46 building intended for human occupancy except when the characteristics of location class 4 prevail. Location class 3 is assigned to describe shopping centres, residential areas, industrial areas etc.
3.10.4 Location Class 4
This is an “advanced location class 3″ used to denote locations where there is heavy traffic, numerous multi-story buildings, and numerous other utilities including underground infrastructures.
3.11 Design Factor
This is a function of the location class as already explained above. It is a factor applied to the wall thickness calculation to provide extra pressure containment resulting from increased wall thickness. As the location class increases the design factor reduces, the reduction in design factor results in a higher calculated pipeline wall thickness.
Below are the design factors extracted from ASME Table 841.1.6-1. Kindly note that the exceptions to the design factors are shown in table 841.1.6-2 of ASME B31.8. These exceptions include compressor station piping, pipelines on bridges, pipeline crossing roads etc. Some of the design factors shown in the exceptions are lesser than the actual design factor for the location class.
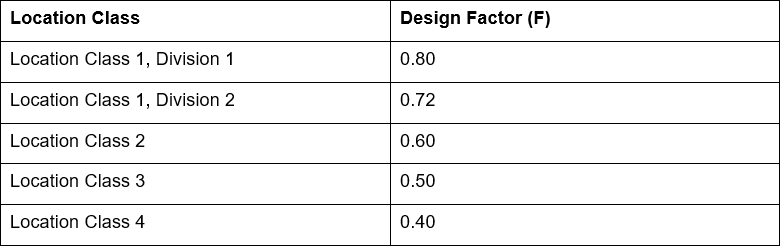
Table 1: Basic Design Factor (F)
3.12 Pipe Wall Thickness Allowance
Allowance is an additional thickness added to the pipe’s calculated wall thickness to cover up for any reduction in wall thickness that may result from manufacturing, handling, or corrosion.
Several allowances are considered in calculating pipeline wall thickness; they include, manufacturing allowance, mechanical allowance, and corrosion allowance.
The manufacturing allowance is mostly taken as zero because most of the pipes manufactured are error-free due to rigorous quality checks performed on pipes.
Corrosion allowance is a function of the fluid to be transported and its effect on the pipe material. Usually, pipes made of stainless steel, duplex stainless steel have a corrosion allowance of zero (0). The corrosion allowance is estimated by predicting the corrosion rate for the entire service years of the pipeline
3.13 Temperature Derating Factor (T)
The temperature derating factor is a factor applied to the wall thickness calculation to compensate for temperature increase. As the steel temperature increases beyond a certain point, the strength begins to reduce; therefore, a factor is included in the calculation to compensate for this strength loss.
The table below shows the temperature derating factors extracted from Table 841.1.8-1 of ASME B31.8. Note for intermediate temperature interpolate for derating factor

Table 2: temperature Derating Factors
4 Material Selection.
Appropriate material must be selected during the pipeline design; some of the basis for selecting material include is fluid to be transported, material resistance to corrosion, material availability, and available grades.
A material engineer performs the material selection, though this can be done by an engineer experienced in this area. There are varieties of materials that are utilised for pipeline construction. The most popular materials are those covered by the API 5L standard. Other carbon steel materials that can be utilised include ASTM A53, ASTM A106, ASTM A333, and ASTM A524.
Details of the characteristics of these materials are shown in the standards governing these materials.
4.1.1 API 5L Material
The API 5L standard covers these materials.
This standard covers the requirements for the manufacture of seamless and welded pipes. There are two products specification levels defined in API 5L PSL 1 (Product specification level 1) and PSL 2 (Product specification Level 2)
In this code, the acceptable chemical composition of pipe materials is defined, acceptable minimum yield strength and tensile strength of pipe materials are stated. Note the yield strength is utilised in wall thickness calculation.
Also shown in this standard are tolerance for pipeline diameter and out-of-roundness, tolerance for wall thickness, etc.
4.1.2 ASTM A106 Material
These materials are covered by the ASTM A106/106M standard. The standard covers seamless carbon steel pipes applicable for high-temperature services (Size NPS 1/8 to NPS 48). This standard defines the material composition, minimum yield, and tensile strength of all material grades (A, B, and C).
4.1.3 ASTM A53 Material
This pipe material is covered by the ASTM A53/53M standard. The standard covers seamless pipes and welded black and hot-dipped galvanised steel pipes (NPS 1/8 to NPS 26). This standard defines the material composition, minimum yield, and tensile strength of all material grades (A and B).
4.2 Material Grade Selection
As defined in section 4.45 of API 5L, pipe grade is the designation of pipe strength level. The higher the grade of a pipe, the higher the strength.
After the material has been selected, an appropriate grade is selected. I have tabulated below some available grades of pipe materials. Table 2 and 3 are extracts from API 5L Table 6 and 7 (Requirements for the results of tensile tests for PSL 1 and PSL 2 pipe), Table 3 is an extract from Table 2 (Tensile requirements) of ASTM A106, while Table 4 is an extract from Table 2 (Tensile Requirements) of ASTM A53.
Generally, low-grade pipe materials (low strength) such as API 5L Grade A25, A25P, A, and ASTM A106 Gr A. are not commonly used as pipeline material.
For other materials refer to applicable codes and standards for strength values.

Table 3: API 5L PSL 1 Pipe Materials Grades and Specified Minimum Yield Strength

Table 4: API 5L PSL 2 Pipe Materials Grades and Specified Minimum Yield Strength

Table 5: ASTM A106 Pipe Materials Grades and Specified Minimum Yield Strength

Table 6: ASTM A106 Pipe Materials Grades and Specified Minimum Yield Strength
4.3 Pipe Yield Strength
The Yield strength is expressed in psi (pounds per square inch) or MPa (Mega Pascal). As defined in section 804.6 of ASME B31.8; this is the strength at which a material exhibits a specified limiting permanent set or produces a specified total elongation under load.
4.4 Specified Minimum Yield Strength (SMYS) of Pipe
The specified minimum yield strength of a pipe expressed in pounds per square inch (psi) or Mega Pascal (MPa) is the minimum yield strength prescribed by the specification under which the pipe is procured/purchased from the manufacturer.
The pipe manufacturer must guarantee the specified minimum yield strength.
The values of the specified minimum yield strength of various pipeline materials grades are stated in various standards. See table 3, 4, 5, and 6 above for values extracted from respective standards.
5 Wall Thickness as Per ASME B31.8
In the previous sections, most of the data utilised for wall thickness calculations have been explained. A typical wall thickness calculation for a pipeline transporting Natural Gas will be performed.
5.1 Wall Thickness Calculation Formula
The wall thickness can be derived from the equation stated in section 841.1.1 of the code. Two formulas are given, one utilises the customary unit while the other SI unit.
Customary Unit
Where
D = Nominal outside diameter of the pipe, in. (mm)
E = Longitudinal Joint Factor obtained from Table 841.1.7-1 [see also para. 817.1.3(d)]
F = Design factor obtained from Table 841.1.6-1.
P = Design pressure, psig (kPa)
S = Specified minimum yield strength, psi (MPa)
CA = Corrosion allowance
Note CA is not included in the equation stated in ASME B31.8, however, CA should be added to the calculated minimum pressure wall thickness calculated for pipelines made of carbon steel materials. Also note that the nomenclature tmin, t etc used in this article are not consistent with those stated in ASME B31.8, they have been used for clarity purpose.
Also, the design factors in ASME B31.8 have been set with due consideration given to under thickness tolerance, therefore these tolerances such as mill tolerance should not be added to the wall thickness calculated.
Selected pipeline wall thickness are as per Table 1 of ASME B36.10M
5.2 Stress Analysis
Stress analysis should be performed on the pipeline after the wall thickness calculation has been calculated. Detailed stress analysis can be performed using software, such as Caesar II. However, spreadsheet or hand calculation can be used for preliminary analysis.
Below are some of the terms associated with pipeline stress analysis. Note the stress analysis should be performed for different cases such as
- Installation case
- Newly installed operational case (Pipeline wall thickness intact)
- End of Life operational case (Wall thickness minus Corrosion allowance)
- Hydrotest case
- Other cases required.
The calculation performed in this article is for the newly installed case.
5.2.1 Stress
This is the force acting per unit area on the pipeline expressed in psi or MPa. Pipelines are subjected to different types of stress, as described below.
5.2.2 Hoop Stress
It is also known as circumferential stress; this is the stress acting circumferentially in a plane perpendicular to the pipeline’s longitudinal axis. This stress is generated by the resultant pressure of the fluid acting on the pipeline. External pressure is neglected for onshore pipelines except for instances like road, rail crossings, or other scenarios’ where the external pressure is significant.
Hoop stress is determined using Barlow’s equation. The equation is presented in section 805.2.3
As shown below
Customary Unit
Note: The above equations may not be applicable for pipe D/t less than 20.
5.2.3 Maximum allowable stress:
This is the maximum stress permitted by the pipeline design code (ASME B31.8). They are defined in various sections of the code.
5.2.4 Bending Stress
This is the force per unit area acting at a point along the pipeline’s length resulting from the bending moment applied at that point.
Buried pipelines are subjected to minimal bending stress. Bending stress can be significantly high during installation, when spanning occurs due to differential settlement.
Stress in straight sections of pipelines or large-radius bends due to weight or other external loads can be estimated using the equation below.
5.2.5 Axial Stress
Axial stress is the stress acting along the axis of the pipe. It can be tensile or compressive.
5.2.5.1 Tensile Stress
This stress act in the longitudinal axis of the pipeline. It is the applied pulling force divided by the original cross-sectional area of the pipeline.
5.2.5.2 Compressive Stress
This is the opposite of tensile stress. This is the applied pushing force divided by the original cross-sectional area.
5.2.6 Thermal Stress
This is the stress imposed on the pipeline resulting from the change in temperature experienced. This is usually significant when the operating temperature is very high compared to the installation temperature.
5.2.7 Operating Stress
This is the stress on the pipeline during its normal operating condition.
5.3 Example
Estimate the thickness of a pipeline intended to convey natural gas from a processing facility to a metering station. The two facilities are located in a densely populated area; therefore, the pipeline will traverse areas of dense population. The pipeline is buried at 1m depth; there are no road, rail, and river crossings.
The following data forms the basis of calculation considerations;
- Pipeline Size (NPS) = 12”
- Pipe Material = API 5L Grade B, PSL 2
- Pipe Material API 5L Gr. B
- Pipe Type = Seamless
- Design Pressure = 19.65 Barg
- Maximum Operating Pressure = 12Barg
- Maximum Design Temperature = 38 °C
- Installation (Backfilled) Temperature = 10 °C (Assumed cold condition for conservatism)
- Corrosion Allowance, (CA) = 3.0 mm
- Modulus of Elasticity of Steel, E = 207 GPA
- Coefficient of Thermal Expansion, α = 11.7 x 10-6 mm/mm/°C
Solution
Pipe nominal Diameter = 12.75” = 323.8mm
Design Pressure = 19.65 Barg = 1965 KPa = 285Psig
SMYS for API 5L Gr. B = 245 MPa = 35500 psi (refer to API 5L, Table 7)
Location Class = 4 (Densely populated area)
Design Factor = 0.4
Pipe Type = Seamless.
Longitudinal Joint Factor (E) = 1.00 (ASME B31.8, Table 841.1.7-1, for API 5L material;
Seamless).
Temperature Derating Factor, T = 1.00 (ASME B31.8, Table 841.1.8-1, for Steel Pipe). Based on the maximum operating temperature of 38oC
Substituting the applicable data into equation (2) above
Stress Calculation (Installation Case)
Pipeline is buried in consolidated soil therefore pipeline is restrained
Hoop Stress
Using equation 5 above
Internal Pressure Longitudinal Stress
The longitudinal stress in pipelines due to internal pressure is calculated using the equation in 833.2 (a)
Thermal expansion longitudinal stress
The longitudinal stress due to thermal expansion in restrained pipelines is calculated using the equation in 833.2 (c)p
Net Longitudinal Stress
The net longitudinal stress excluding bending and axial stress is calculated using the equation in 833.3.
Note axial stress is considered zero (0) because no axial load is applied to the pipeline. Axial stress is significant when a pipeline is installed using HDD and other methodology that entails applying a tensile or compressive force on the pipeline. Bending stress is usually negligible for straight sections of pipelines installed in consolidated soil. However, bending stress can be high during installation. The bending stress during installation is minimised by controlling the elastic bend radius of the pipeline. The elastic bending radius is calculated from the estimated margin for elastic bending stress.
Allowable Longitudinal Stress Check
Refer to section 833.3 (b) the permissible SL is evaluated using the equation below.
Combined Stress
Refer section 833.4 the combined biaxial stress state of a pipeline in the operating mode can be estimated using either equation below.
Allowable Equivalent Stress Check
Refer to section 833.4(a) the permissible equivalent stress is evaluated using the equation below.
6 References
- API 5L: Specification for Line Pipe
- ASME B31.4: Pipeline Transportation Systems for Liquids and Slurries
- ASTM A53: Standard Specification for Pipe, Steel, Black and Hot-Dipped, Zinc-Coated, Welded andSeamless1
- AST A106: Standard Specification for Seamless Carbon Steel Pipe for High-Temperature Service1
- ASME B31.8: Gas Transmission and Distribution Piping Systems
- CSA Z662: Oil and Gas Pipeline Systems
- PD 8010 Part 1 & 2: Code of Practice for Pipelines
- ISO 13623: Petroleum and Natural Gas Industries — Pipeline Transportation Systems