1 Introduction
Hot tapping is a technique for connecting a mechanical or soldered branch fitting to in-service piping or equipment and drilling or cutting a part of the pipe or equipment within the connected fitting to create an aperture. Forming a new connection to an already pressurized pipe or vessel without halting or emptying that segment of pipe or vessel is known as hot tapping. This implies that a pipeline can keep running while maintenance or repairs are being carried out.
In the hydrocarbon industry, hot tapping is widely used. Due to the delays in product supply to clients and other facilities, shutting down pipelines is typically challenging. A hot tap can connect new links to an already operational pipeline without disrupting the flow. It can also be used in conjunction with line plugging to redirect circulation around a line or piping segment that is being repaired or maintained.[1]
2 Critical Requirements
A hot tapping procedure is a high-risk activity that should not be performed on a regular basis. It must only be carried out if a facility closure is not possible – an evaluation that takes into account a variety of factors,[2] including:
- Hot tapping entails hot labour, such as welding on operational pipes, piping, or tanks. As a result, a thorough assessment of the hazards of hot work is required. Every hot tapping procedure requires the highest level of safety. Hot tapping should not be done until the safety of the employees and the environment can be assured. In the event of a hot tap failure, the dangers described here include pollution and the discharge of dangerous substances.
- The pipes, pipeline, or reservoir to be tapped should be in good working order. To evaluate if the hot tap is safe to operate, the integrity of the machinery or pipes must be carefully examined. It is forbidden to tap equipment or pipes that have degraded beyond a certain point.
- The system must be configured in such a way that hot tapping may be done without difficulty. For piping layouts and tanks, this is frequently a more important criterion than for pipelines. The hot tap should not be done if accessibility to the lines is restricted. This covers things like soil condition, water tables, and plant overgrowth, among other things.
- Hot tapping has a number of operating restrictions, including fluid temperature, pressure, flow velocity, and so on, as will be explained later. To guarantee that hot tapping may be effectively done within these constraints, the system’s operational data must be closely examined.
- The machine used to execute the hot tap should be capable of effectively completing the task. The choice of equipment is critical since the improper machine can lead to an unsuccessful hot tapping procedure. Temperature, pressure, flow rate, and other operational requirements must all be met by the machine. Hot tapping should not be done if a machine capable of operating efficiently under all defined circumstances is not available.
- The hot tap operation’s financial element must be properly assessed. It’s best to avoid situations when the expense of a hot tap is much greater than the expense of shutting down and doing normal maintenance.
- Is it possible to safely weld the hot tapping fitting onto the pipeline? Is it possible to weld a pipeline under the working circumstances and with the materials of the container or pipeline? Before executing a hot tap, this must be justified.
- Before executing any hot tapping operation, all requirements (industry codes, municipal ordinances, etc.) must be thoroughly assessed, and the operation must not continue if the requirements are not satisfied.

Figure 1 Hot Tap Process
3 Documentation Requirements
Before carrying out a hot tap, careful planning and design must be carried out. This will require creating several documents for the customer and other stakeholders to examine and approve. The following are some of the documents to prepare:
- Documentation for the design. Reports on material selection, wall thickness calculations, and so on. The design and material report must include the rationale for choosing the materials, as well as the material’s compatibility with the pipe, corrosion resistance, and other factors.
- The designs to be created will contain overall pipe network layout drawings, sections and details, and so on.
- Take-off of materials. This is a paper that will help you obtain all of the items you’ll need to complete the hot tap effectively. It will list the necessary quantity of faucets, nuts and bolts, couplings, and pipes for branch connections, among other things.
- A complete Job Hazard Analysis must be included in the safety plan and documentation. At a bare minimum, the safety plan should include escape routes, firefighting equipment, safety equipment, gas detectors, and first-aid facilities.
- Procedures for transportation. This section will describe how well the hot tap equipment, components, and workers will be delivered from and to the job site. This is especially important if the hot tapping is in a remote or difficult-to-reach place.
- Procedures for preparing the site. The land must be cleared for hot tap installations in busy regions. Temporary roadways will be built if there is no accessible roadway towards the hot tap site (if feasible). For subterranean pipes, excavation surrounding the pipeline is required.
- The protocol should include broad data about the activities, such as the tap angle and machine operating technique, among other things.
- Procedures for welding The welding method is a crucial document that specifies the kind of welding, the electrodes to be used, the welding current, preheating requirements, soldering temperature, welding machines, and so on.
- Procedures for non-destructive testing (NDT). This document will normally describe how the welded joints’ integrity will be verified. It might include things like the hydro test, UT, MPI, and so on.
- This might be included in the NDT protocol or it could be a separate document. This will display the test pressure, the medium to utilize for the test, the test period, and so on.
- A list of all the tasks that must be accomplished prior to the start of the hot tapping process. It’s frequently in the form of a table, with actions ticked off and the people responsible listed.
- Close-out report on hot tapping. The closure report is a breakdown of all tasks completed, as well as a summary of learned lessons, after a successful hot tap.
4 Safety Requirements
Although hot tapping technology has advanced significantly over time, there are still a number of limits in place to ensure the process’s safety. It should be emphasized that these limitations differ per company and are also reliant on the capabilities of hot tap equipment and staff.[3]
In most cases, hot tapping should be avoided on:
- Heat exchangers or compressed gases that hold a combination of combustible gases and air Pipelines, pipework, or storage facilities that carry a combination of dangerous gas and air
- Encased storage tanks or pipe that has to be heated after welding. If post-weld heat treatment is necessary, more study and consultation with experts must be conducted.
- Storage tanks and pipelines store unsaturated hydrocarbons that decompose exothermically owing to high temperatures generated by welding operations. Ethylene, propylene, and other hydrocarbons are examples of these hydrocarbons.
- Storage tank decks, roofs, floating roofs, and pontoons.
- Pipes or tanks that have been clad, unless they have been authorised following a thorough inspection by trained professionals. Hot tapping, on the other hand, can be done on pipes or equipment that are internally flow coated.
- Unless the customer permits it after a rigorous appraisal of the tapping operation, do not tap pipes or containers when the liquid content is below 0 Celsius (32 Fahrenheit) or beyond 200 Celsius (392 Fahrenheit).
- Unless a comprehensive assessment by engineers, equipment under pressure, i.e. pressure less than atmospheric pressure Machinery and pipes carrying hazardous materials.
5 Hot Tap Requirements
Before completing a hot tapping procedure, this section emphasizes some of the most important prerequisites. Though every hot tapping process is distinctive and should be assessed on its own merits, these factors provide a good starting point.
5.1 Pipeline Requirements
The most prevalent sort of hot tapping activity is tapping into pipelines and pipework. The following are some requirements:
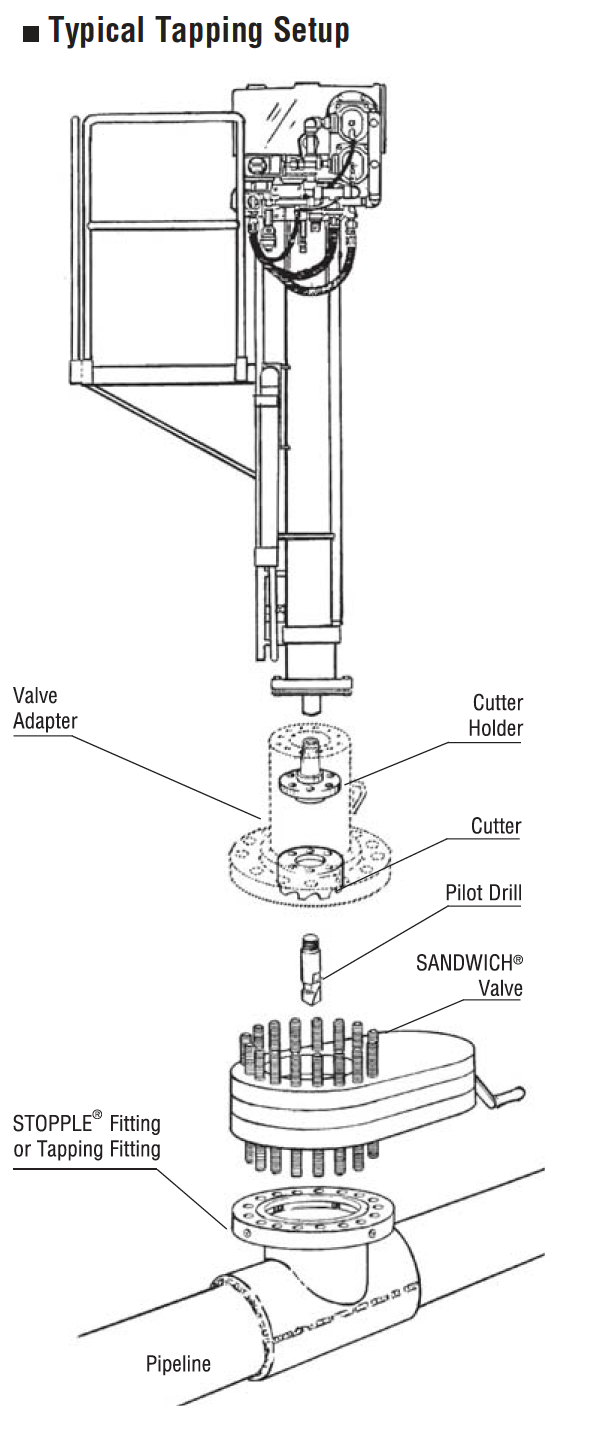
Figure 2 Pipeline Hot Tap
- The pipe materials and fittings used in the hot tapping process must be suitable for the run pipe’s material.
- The pipelines and fittings must have a rating that is equivalent to or greater than the current run pipe.
- An expert engineer must create and review welding procedures to ensure that the soldering can be completed effectively on the line or pipes.
- Hot tapping should be done on horizontal pipes in a vertically downward position. A full job risk assessment and technical study must be completed before a slanted hot tap is done.
- Flare lines should not be hot tapped or welded since there is a risk of oxygen infiltration, which might result in the production of a combustible combination. If tapping is required on flare lines, the line must be checked for oxygen intrusion; if this cannot be done, the pipe must be constantly treated with inert carrier gas or water during the welding process. Gas detectors must be used to detect oxygen and other dangerous gas ingresses on a continuous basis.
5.2 Tank Requirements
Welding on the outside of a container or tank poses the greatest risk of igniting a flammable environment in the vapour region just above the liquid surface. Additional parameters must be met in order to effectively execute a hot tap into a tank or vessel. The following are some of these requirements:
- Welding on the outside of the tanks is not permitted unless a system is in place on the floor to avoid combustible gases from entering the welding area. Gas detection devices that are reliable must be placed in a strategic area. When gas or vapour is found, work must be promptly halted.
- Tank venting that may move vapour around the area where welding is done. As a result of the vapour, a combustible environment forms surrounding the welding site.
- Overflowing of goods in the tank, resulting in product spilling onto the welding area.
- Allowing the volume of fluid in the tank to go under the welding point inadvertently. The welding region is a specified zone around the weld site, not just the immediate place of welding. When the temperature of the liquid in the tank drops below the welding point, the heat sink supplied by the liquid is eliminated, exposing the vapour space in the tank to the welding point and potentially igniting it.
- Welding must be done by qualified workers, ideally those who have worked on live pipes before.
- Burn-through of the container or tank wall must be avoided during welding. Adequate safeguards, such as temperature regulation, must be implemented.
- Activities such as hot tap or welding are not permitted on floating rooftops, pontoons, or decks. Flammability dangers exist in certain locations of a tank.
5.3 Welding Requirements
For soldering work in a hot tap, a welding technique must be designed. All welders must be qualified according to the relevant standards and requirements. Welders with prior experience may be given preference. Welding should not be authorised closer than inches of flanges or threaded connection, or roughly 3 inches to a welded seam unless judged acceptable by an engineering assessment. Before connecting the hot tap machine, all welds must be visually examined and tested. Pressure tests may be performed to evaluate weld integrity instead of dye penetrant testing, ultrasonic inspection, or magnetic particle inspection (MPI).
To ensure the integrity of welded joints, they must be tested. A hydro test should be performed to test welded connections according to applicable regulations if the heat of the piping, pipeline, or tank allows it. The test level should be at least 10% higher than the pressure range; nevertheless, if an internal breakdown is expected, the test pressure should not be more than 10% of the operational pressure. According to appropriate codes, the test pressure may be lowered. If the temperatures do not allow for a hydro test, the weld may be treated with air or nitrogen mixed with a soap solution.[4]
5.4 Load Requirements:
When doing hot tapping, outside loads are a major problem. The impact of external loads on the pipe must be properly assessed and reduced. When hot tapping, the weight of the equipment and the people doing the work may be distributed evenly or unevenly on the pipeline, resulting in pipeline failure. To counteract the influence of external loads, all pipes be hot tapped should be suitably supported. Additionally, the damaged pipeline should be used while doing this assessment.[5]
5.5 Temperature Requirements:
Both the hot tapping equipment, the fittings, and the pipeline must be kept at a safe temperature. There are also are hot tap devices that can withstand temperatures of up to 300 degrees Celsius.
Qualified workers must examine the highest metal temperature arising from the hot tapping procedure. Prior to beginning welding activities, the minimum ambient temperature should be determined. Welding should not be done when the ambient temperature is below -50°F (-45°C) unless specific precautions are followed, as indicated. Provision of temporary welding shelter and space heaters are among these safeguards.
A welding technique must be created, specifying whether or not preheating is necessary, as well as the electrodes that will be used for welding.
It is necessary to determine the maximum temperature that can be reached as a result of welding. This will be calculated based on the pipe’s actual wall thickness. The maximum temperature must take the reactivity of the fluid being conveyed into account.[6]
5.6 Location Requirements
It’s critical to pick the right spot for the hot tap. Locations for hot taps must be easily approachable and free of impediments. If there are filters, strainers, or traps placed downstream of the hot tap position before the equipment, hot tapping may only be done upstream of moving equipment (pumps, compressors, etc.).
6 Hot Tap Machine
In contexts of temperature and pressure, hot tap machines will be rated appropriately. To guarantee that the coupon is cut continuously, the hot tap machine must be positioned on the valves and connected with the fitting.
The total travel distance of the equipment is an important feature to consider when choosing a machine. Each machine has its own version of this.
It must be ensured that the chosen machine can travel the appropriate length from the hot tap valves until the full coupon is cut before hot tapping may begin.
The formula below may be used to calculate the total travel distance. This calculation should be tweaked to fit the needs of each application. Assume the Cutter’s position right after cutting the full coupon and a short distance to ensure that the coupon has been cut.[7]

Figure 3 Hot Tap Distance
7 References
[1] C. Herckis, “Understanding hot tapping and plugging as an effective procedure to facilitate relocation, repair, or modification of water infrastructure when uninterrupted operation is necessary,” in Pipelines 2018: Utility Engineering, Surveying, and Multidisciplinary Topics: American Society of Civil Engineers Reston, VA, 2018, pp. 63-73.
[2] C. Herckis, “Hot Tapping and Plugging in New York City: A Method to Maintain Service and Protect the Marine Environment during Reconstruction of a Major Sewage Pumping Station and Treatment Plant,” in Pipelines 2011: A Sound Conduit for Sharing Solutions, 2011, pp. 372-381.
[3] C. Herckis, “In Service Welding and Hot Tapping and Plugging Enable Operational Safety of High-Pressure Natural Gas Transmission Line River Crossings in Bolivia and Mexico,” in Pipelines 2013: Pipelines and Trenchless Construction and Renewals—A Global Perspective, 2013, pp. 1620-1634.
[4] R. Felix, W. Bruce, and P. Threadgill, “Development of procedures for hot tap welding onto sour service pipelines,” in International Arctic Technology Conference, 1991: OnePetro.
[5] D. J. J. P. G. J. Hicks, “Guidelines for welding on pressurized pipe,” vol. 210, no. 3, 1983.
[6] H. W. Mishler and J. J. O. G. J. Kiefner, “Study compares hot-tap welding methods,” vol. 79, 1981.
[7] Y. Ogayu, “Confirmation of Validity of Hot Tapping Welding,” in ASME Pressure Vessels and Piping Conference, 2009, vol. 43703, pp. 175-179.