1 Refrigeration
1.1 Description of System
A refrigeration system is a combination of equipment and piping connected in a sequential order to produce a cooling effect, i.e. the process of extracting heat from a lower temperature heat source, a substance or refrigerating medium and transferring it to a higher temperature heat sink, commonly atmospheric air and surface water, in order to maintain the temperature of the heat source below that of the surroundings.
Refrigeration systems can be classified into the following categories:
- Chilling and chilled storage. The common temperature range is from 0 to 10 ◦ C.
- Freezing, deep freezing, cold storage and deep cold. The expected temperature range is from 0 to minus 40 ◦ C.
Chilled-water systems consist of these functional parts:
- Chillers that cool the water or fluid
- Condenser-water pumps, cooling towers or condenser fans, and pipes that reject heat from the chiller to ambient air
- Loads, often given by coils, that transfer heat from air to water
- Distribution pipes and pumps that send chilled water to the loads
- Controls that integrate the operation of the mechanical components together as a system
As there are numerous and versatile industrial processes requiring refrigeration, there are also different manners of connecting the components and equipment in a refrigeration system. Figure 1 depicts a refrigeration system used in the textile industry for supplying air washers. This particular example will describe the principles of the operation of refrigeration systems [1].

Figure 1. A sample refrigeration system. Source: https://doi.org/10.1002/9780470714379.ch11
The task of this refrigeration system is to produce chilled water with an initial temperature of, let’s say, 10 ◦C, while the design return water temperature could be 15 ◦C. There is a flow of this water in the evaporators of chillers measured in m3/h. The total installed refrigeration capacity is around 8,000 — this can be achieved with given temperatures of chilled water and condensers’ inlet/outlet water temperatures of 30/35 ◦C. The flow rates of chillers condensers are also given in m3/h. Typically, the refrigerant was R-11 or trichloromonofluoromethane (CCl3F). Although refrigerant R-11 is considered a safe product as it is non-flammable and non-explosive, its use has been restricted by some problems: low operating pressures and high potential to deplete the ozone layer.
The electrical power of the electric motors for running the turbo compressors of the chillers resides between 300 kW and 500 kW. In a regular plant, most chillers are anticipated to operate while one or two are used as a stand-by reserve. In addition to that, the power of the pumps for running water for the cooling tower can reach 45 kW each, evaporators pumps 22 kW each, and water supply pumps 55 kW each. The total installed power of the pumps will depend on the total number of pumps, as well as the installed power for driving the ventilators of the cooling towers.
The illustrated refrigeration system is undoubtedly a considerable consumer of electric power. We are interested mainly in the performance and overall energy efficiency of the refrigerating system, which besides chillers, also includes pumps, cooling towers, maintenance, manner of administration, outside temperatures and relative humidity, load variations, etc. All of these factors have a significant impact on the system’s operational requirements and energy consumption.
1.2 Primary and Secondary Components
Chiller
There is a variety of water chiller types. Most commonly, these are absorption, helical rotary, centrifugal, and scroll; some reciprocating configurations are also available. Chillers can be either air- or water-cooled. Major vapour-compression chiller components include an evaporator, one or more compressors, condenser, and expansion devices. Generally, water-cooled models are typically installed indoors, while air-cooled chillers are outdoors—either on the roof or next to the building. Air-cooled chillers may have a distant evaporator inside the building for freeze protection in frosty environments. The evaporator segment of a water chiller is a shell-and-tube, refrigerant-to-water heat exchanger. Subject to the chiller’s design, either the refrigerant or the water is contained within the tubes.
To cool a process or building, the excess heat must ultimately be rejected outside or to another system (heat recovery). The total amount of thermal energy rejected takes account of the sum of the evaporator load, the compressor work, and the motor inefficiency. Whereas in an open chiller with the motor separated from the compressor — and connected by a shaft — the motor heat is rejected directly to the surrounding air, in a hermetic chiller —the motor and compressor are in the same housing — these loads are all rejected through the condenser. The compressor work and the evaporator load are released through the condenser, and the motor heat must be handled by the equipment room’s air-conditioning system.
Otherwise, air-cooled chillers do not use condenser water; instead, they liberate heat by passing ambient air across heat exchangers. In the case of packaged air-cooled chillers, the manufacturers improve performance by staging fans in response to ambient, dry-bulb temperature and chiller load. Air-cooled chillers can also be split apart. The first distinguishing feature between air-cooled and water-cooled chillers is their available capacity. Packaged chillers with air-cooled condensers typically range from 7.5 to 500 tons. The capacity of packaged water-cooled chillers ranges from 10 to approximately 4,000 tons.
Loads
Air handlers are frequently used to meet cooling demands in comfort-cooling applications, as long as they incorporate coils to transfer heat from conditioned room air to circulating chilled water. As air passes over the finned surface of the cooling coils, it is cooled and dehumidified. Because the psychrometric process of air conditioning takes place at the coils, choosing the right size and type among the many options available is critical for proper system performance. Cooling air isn’t really required for some particular process loads. Instead, they may entail direct heat transfer within a piece of process equipment, such as an injection-moulding machine’s cooling jacket.
Distribution System
Cold water is circulated through fixed piping—most commonly copper, steel, or plastic—that couples the chiller with various load terminals. Piping is sized to meet construction cost, pressure loss, and water velocity parameters. The native pump creates pressure to circulate chilled water within the loop. Normally, the pump must overcome the frictional pressure losses caused by the components already described and the pressure differential across open control valves. The chilled-water pump is usually located upstream of the chiller.

Figure 2. Variable primary system. Source: https://www.bcxa.org/
By itself, the distribution system is clear to comprehend. A streamlined distribution system consists of multiple cooling coils, each governed by a thermostat that controls the flow in its respective spiral. The valves may be either two-way or three-way. The pump may ride its curve as flow fluctuates or use a flow control method such as a variable-speed drive. The distribution arrangement may contain other elements, such as an expansion tank, an air separator, control, balancing, or check valves, to name a few. The water density (and volume) in a “closed” chilled-water distribution system fluctuates as it undergoes changes in temperature. The expansion tank allows for this augmentation and contraction of water volume.
Condenser-Water System
To cast off heat, water is passed through a cooling tower where a fraction of it evaporates, thus cooling the remaining water. The effectiveness of a particular cooling tower at transferring heat depends on the previously mentioned conditions, namely water temperature, ambient wet bulb, and water flow rate. During many points of operation, the optimal output is not the lowest water temperature the cooling tower can produce. It is important for the system designer and field worker in charge to examine the use of system-level panels to fix the tower-sump temperature setpoint to reduce the sum of chiller-plus-tower energy. A proper chiller-plant management system can automatise the chiller-tower control [2].
Pressure drop through the chiller’s condenser and piping, plus the cooling tower static lift, is overcome by using a condenser-water pump. The condenser-heat exchange surfaces must be kept free of scale and sludge to ensure optimum heat transfer performance.
2 Hot Water
2.1 Hot Water: For What?
Hot water is an essential requirement for all dwellings and most working environments. The following factors should be considered in the selection and design of hot water supply systems:
- quantity of hot water required;
- temperature in storage and at outlets;
- cost of installation and maintenance;
- fuel energy requirements and running costs;
- waste of water and energy;
- user safety.
Domestic hot water service is the generation and delivery of hot water for consumption at outlets such as sinks, baths, showers, dishwashers, etc. Although the water supplied is not required to be potable, it will still be used for washing and so must be delivered in a hygienic and pleasant condition at the point of use. In particular, great care needs to be taken to prevent bacterial growth such as legionella. As biocides cannot be added, high temperatures need to be maintained, though not so high as to risk scalding.
There are many methods of supplying hot water, ranging from simple gas or electric single point arrangement for one outlet to the more complex centralised boiler systems supplying hot water to several outlets. Heat pump systems for water heating and hot water supply can be carried out using multiple low-temperature energy sources. The advantages of such systems are illustrated by the example of a heat pump system using earth (or ground) heat for the heat supply of a railway station. The system utilises the natural heat of the ground and provides water heating for a passenger waiting room and offices in the cold season, air conditioning in office rooms in summer, and hot water supply throughout the year.
The system’s design must also allow for the expansion of the water to prevent explosions. Regulations and codes of practice cover these safety requirements. Hot water systems consume significant quantities of both water and energy, and these are also dealt with in various regulations.
A heat pump water heater uses less energy than an electric water heater for the same thermal output. Generally, the vapour-compression heat pump is used for water heating and the working fluids used are chlorofluorocarbon (CFC), hydrochlorofluorocarbon (HCFC) and hydrofluorocarbon (HFC) refrigerants. Recently, natural fluids have been considered to replace the HCFC and HFC refrigerants, which are harmful to the environment. Carbon dioxide is one of the promising natural fluids. It is inexpensive, nontoxic and available on the market.
2.2 Instantaneous Versus Storage
The heat (energy) required to raise the temperature of water is given by the well-known equation:
where M is the mass of the water, (kg); Cpw is the specific heat of water, (4.18kJ/kgK); is the rise in water temperature (K), when the energy, E, is given in kJ. The power (rate of energy supplied) to achieve this in a given time period, t is then:
This equation is directly applicable to heating a fixed mass of water in a storage vessel. However, it can easily be modified for water flow by noting that the fraction M/ is the same as the mass flow rate.
So, for an instantaneous HWS system:
where is the mass flow rate of the water (kg/s).
It is revealing to compare the power requirements of storage and instantaneous systems. For example, a 22mm tap serving a bath has a maximum flow rate of up to about 0.3kg/s (note that 1kg of water is approximately 1 litre). A typical delivery temperature is 55°C. In winter, the water may enter the system at 10°C. This gives an instantaneous demand of some 56kW. Yet domestic storage systems are quite capable of supplying a hot bath using a mere 3kW electric immersion heater. Obviously, an electric instantaneous water heater to serve a bath is out of the question. Such high heat output rates would also be uneconomic for domestic gas-fired water heaters.
Domestic combination boilers are limited to a HWS output of about 20kW. Spray taps are frequently used for wash hand basins in non-domestic buildings because of their very low rate, only about 0.015kg/s. As well as helping to conserve water, a 3kW instantaneous electric heater is just sufficient to heat the water to an acceptable temperature for a single tap. Even so, peak electrical demand would be high in a building containing many such taps.
One disadvantage of the storage system is that it takes a finite time to reach the design temperature once all the hot water has been run off. This is known as the recovery time and depends on the mass of water stored and the power of the heating element. Equations can be arranged to give the typical recovery time of a domestic hot water cylinder (125kg water capacity) based on a 3kW immersion heater for a 50K lift in temperature (storage temperatures will be discussed later): t = 8700s or about two and a half hours. This is rather a long time. Domestic immersion heaters are limited to 3kW for practical reasons regarding the design and cost of domestic electrical distribution installations. When the boiler serves the HWS cylinder, the heat exchanger is rated at about 6kW to give a recovery time of nearer one hour [3]. Instantaneous systems do not suffer from this problem. Although the water flow rate is limited, it is always available.
The second drawback of storage systems is that they occupy more space. The designer could decide to install a smaller storage vessel. For the same heat exchanger duty, this would result in shorter recovery times but would increase the number of times each day when hot water was not available. Alternatively, a larger vessel could be installed of sufficient capacity to allow it to meet the maximum demand during the day with continuous recovery.
The size of domestic hot water cylinders has become very much standardised, being a compromise between physical space requirements and hot water availability. For non-domestic HWS, the range of sizes of storage vessels and LPHW heat exchangers available is considerable. Some designers have opted for large storage volumes in the past, but an increasingly common system nowadays is the ‘hot water generator’. This has a small water storage volume to meet maximum demand for a few minutes combined with a direct, gas-fired heater to give very short recovery times. Guidance on how to select appropriate storage volumes and heat exchanger duties is given in manuals, handbooks, scientific literature, and other technical documents.
2.3 Non-Domestic Heat Storage
The waiting time at taps for acceptably hot water to reach the user has a further economic implication in commercial buildings: loss of workforce productivity. In order to reduce waiting time, water must be available within the pipework at acceptable temperatures at all times (during occupancy). Further, legionella is a major concern and maintaining a high water temperature in all parts of the pipework will reduce the risk. As insulation will only slow down the cooling rate of the water and not stop it, other measures are needed.
There are two approaches: trace heating of the pipework or continuous water circulation. In both cases, reasonable standards of insulation are still required. A typical system utilises a return circuit. The system is designed to provide a continuous flow of hot water around the circuit, just sufficient to prevent the water temperature at the furthest tap from the cylinder from falling below the required value. A small pump generates the flow rate. The return pipe is connected to the end of each supply branch so that there is a continuous circulation of water through all branches. It would be impracticable to provide a constant circulation through pipes serving an individual tap.
In designing a storage system, gravity (or in unvented systems, mains pressure) provides the flow to the taps. Pipework must therefore be sized with this available pressure in mind. On extensive systems, the available head per metre of pipe can be relatively small, resulting in large diameter pipework being required if the desired flow rates are to be achieved. This increases both capital costs and heat loss rate. It may be cost-effective to utilise a pumped system with more economically sized pipework in such instances. The pump will need to be able to provide the peak demand flow rate while, for much of the time, having to operate at significantly reduced duty. A boosted pump set complete with a small expansion vessel (as is used on boosted cold water systems) may be worth considering for trace heated systems.
2.4 Solar Hot Water
At least for domestic buildings, solar hot water is slowly becoming more popular worldwide. This, it must be said, is because of environmental concerns and the desire to save primary energy and reduce CO2 emissions. Even in often cloudy weather conditions, solar panels can easily contribute 50% or more of the annual hot water requirements of dwellings [4].
Generally, the solar hot water system consists of three main parts: a collection device, a storage facility and a distribution system. The material of the double tube outside is glass for that it is pervious to light, and it holds vacuum better and longer [5]. During sunny days, direct and diffuse light (including the light reflected by the aluminium layer below evacuated tubes) firstly strikes the glass tube. It is converted into heat energy by dark selective coating, absorbing most solar radiation with a low reflection level.
Then the heat is transferred to the copper U-pipe through an aluminium fin, pasted into the inner tube inside. The structure of high vacuum space between the outer tube and inner tube ensures excellent insulation and cut heat losses caused by conduction and convection. Therefore, the fluid temperature can rapidly increase, even exceeding 100°C. However, the fluid will not be boiled so quickly because the high pressure inside the pipes makes the boiling point higher than pure water.
Despite the advantage of vacuum and glass allowing high absorption and low reflection, they make the evacuated tubes seem more fragile. However, the strong cylinder shape can be a feasible solution due to its high tolerance to pressure.
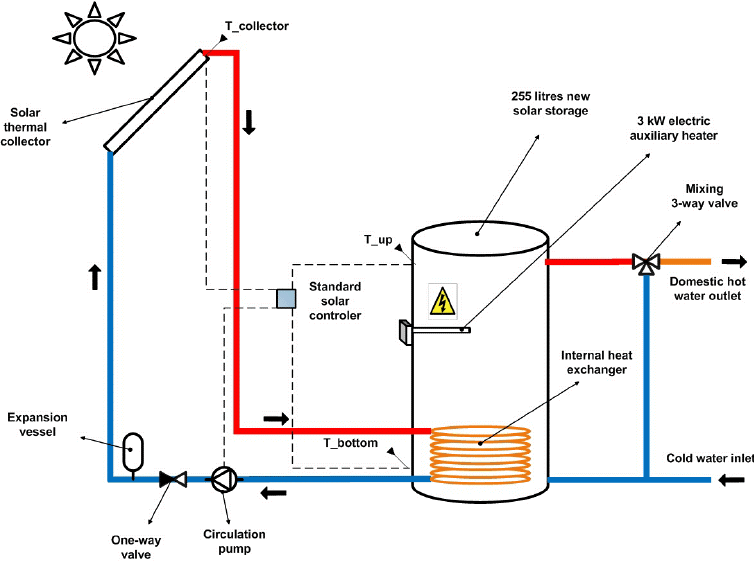
Figure 3. A Standard solar water heating system. Source: https://www.researchgate.net/figure/Standard-solar-water-heating-system_fig1_272646658
Despite the solar energy being free, the efficiency of the panel is still vital as it reduces the area of panels needed and, therefore, capital cost. There may also be limitations on the roof area available and suitable for siting the panel. This needs to be predominantly north-facing (in the southern hemisphere) and at an angle between 30° and 60° to the horizontal. It should also not be shaded by trees and other buildings.
Today, retrofitting domestic hot water systems commonly connects the existing system with new solar storage upstream and uses the existing hot water boiler as a backup heater. Some retrofitted systems make use of thermo-syphoning and are therefore dependent on new well-performing storage for that purpose. Existing installations are often oversized in volume since large design loads have been used before and because domestic hot water consumption has decreased.
Combined with low levels of insulation, such oversizing causes significant system heat losses. When using the existing storage as solar hot water storage, the thermal losses in the system can be decreased since the solar water temperature is lower than the backup temperature. In cases where it is possible to know when the existing boiler is close to the end of its lifetime, it can be advantageous to change the current storage.
3 Flow & Pump Aspects
3.1 Water Flow in Chillers
As the chilled-water temperature rises, so do the refrigerant temperature and pressure for a given chiller. Conversely, as the leaving chilled-water temperature drops, the refrigerant temperature and pressure must also drop. The outcome of leaving chilled-water temperature change on power consumption can be 1.8 to 4.0 per cent per degree Celsius. Always consider the work the compressor must do and the energy demand of the entire system—not only the chiller. It is worth remembering that although reducing leaving chilled-water temperature makes the chiller pay, it may reduce the overall system energy demand because less water is pumped through the system.
The evaporator is reactive to the water flow rate. Excessive flow may result in erosion, vibration, or noise due to high water velocity. But insufficient flow reduces heat-transfer effectiveness and causes poor chiller performance. Some designers are concerned about fouling caused by low flow rates. These concerns are unnecessary since the chilled-water circuit is a closed system, thus reducing the chances of materials entering the system and causing fouling [6]. Chilled water flow through the evaporator must be kept within the specified minimum and maximum limits.
Some chiller controls can accommodate minimal flow variation during machine operation. Other, more sophisticated, allow some flow variation. Some chillers can handle flow rate changes of up to 50% per minute or more, while others can only handle up to 2% per minute. It’s critical to match chiller capabilities to system needs. Before altering the flow through the evaporator in a chiller, contact the manufacturer to find out what the maximum rate of flow variation is.
Besides, the condenser itself is also sensitive to the water flow rate. The causes and effects are similar to those mentioned above for the evaporator. For that reason, condenser-water flow through the chiller should be kept within a specific range of limits, except during transient startup conditions. Long-term fouling of the condenser tubes can occur if the water velocity through the tubes is far too low for extended periods of time and that water is particularly hard. A study testing many internally-enhanced condenser tubes at low speed (around 1.07 m/s) and high water hardness found that this phenomenon is not expected in commercial installations. Employing best maintenance practices and water quality control, all of the tubes tested were probably suitable for long-term-fouling applications.
3.2 Load Heat Transfer
Heat transferred from the loads can be regulated in a few different ways:
Three-way valve
A three-way control valve regulates the volume of water passing through a coil in response to loads. The valve diverts unused water around the coil and requires a steady flow of water in the system, regardless of load. The temperature of the fluid leaving the three-way valve is reduced at part-load conditions, which is a disadvantage of this bypass and can be a major contributor to the so-called “low ΔT syndrome”. Three-way valves are deployed in many existing systems, especially those with constant-volume pumping.

Figure 4. Schematic representation of a three-way valve. Source: https://www.tranebelgium.com/files/book-doc/12/fr/12.1hp13yp1.pdf
Two-way valve
A two-way flow modulating valve at the coil performs the same water throttling function as the three-way valve described above. The twisted wire sees no difference between these two methods; the chilled-water system, however, does. In the case of the two-way valve, all flow in the coil circuit is strangled, so no water is bypassed. Thus, a system using two-way valves is a variable-flow chilled-water system. The water temperature leaving the coil is not diluted by bypass flow, so at part-load conditions, the system return-water thermal load is higher than with three-way valve control.
Variable-speed pump
Using a pump for each coil, the flow may be tuned by adjusting the pump speed. There may be no restraint valves at the coil in such systems, which lowers the cost of the valve and its installation but raises the fee of the coil pump and maintenance.
Face-and-bypass dampers
Control variation could also be performed through an uncontrolled or “wild” coil. In this configuration, control of the conditioned air supply is achieved by employing face- and bypass dampers that let a portion of the air bypass the coil surface. Advantages of this scheme are the suppression of control valves and improved part-load dehumidification. A disadvantage is that all the water is pumped continuously; however, this arrangement may still work economically in systems with very small water pressure drops.
3.3 Chiller-Tower-Pump Balance
Most water-cooled, chilled-water systems use a constant condenser water flow rate. The condenser water flow rate, on the other hand, can be adjusted between the chiller’s minimum and maximum flows. But reducing the condenser water flow rate affects the pumps, chiller, and cooling tower power consumption, as described in this subsection.
Pump power for the condenser water pump is reduced since the flow rate and pressure drop through the pipes and condenser are both reduced. Compressor power is raised because the temperature of the water exiting the condenser rises as the flow rate falls. This increases the compressor lift and, as a result, its energy consumption at a given load.
As previously stated, the water returning to the cooling tower is at a higher temperature. The heat exchanger’s efficiency improves as a result. However, the water flow rate is reduced, either boosting or diminishing the cooling tower’s efficacy. As a result, lowering the flow rate through the cooling tower reduces or increases energy use depending on the load.

Figure 5. A set of cooling towers. Source: https://waterchillers.com/blog/post/how-cooling-tower-vs-chillers-work
3.4 Condenser-water pumping arrangements
Water-cooled chillers need condenser-water-system variations to be acknowledged. Most important, the pump inlet must have a sufficient net positive head, and this often involves locating the pump beneath the cooling-tower sump.
In some applications, each chiller has a dedicated tower. This is most likely to take place when chillers, and their complementary cooling towers, are acquired at different times during the facility’s life—such as when add-ons are completed. A much-used arrangement has a solitary cooling-tower sump with manifolded pumps, one condenser water line, and separate, smaller pipes for each chiller. This offers a number of pros: pumping redundancy, any cooling-tower cell can run with any chiller (as long as cooling towers cells are isolated), hydraulics are generally more straightforward than on the chilled-water side, among others.
3.5 Geothermal Heat Pumps
Heat pumps are devices that force heat flowing from a low-temperature medium to a high-temperature medium. Geothermal-heat pumps, in particular, make use of the underground to extract or inject heat from or to it. A geothermal heat pump system is typically composed of a ground loop tubing that passes through the geothermal well, transferring energy to a circulating fluid (usually a high-concentration solution of salt called brine), a heat pump and a heat distribution system. Pumps circulate water and brine.
The heat pump of a typical off-grid system extracts heat from the brine and transfers it to a hot water thermal energy storage system (TESS). The heat extracted from the brine can either come from the geothermal well or from a cold-water TESS. Hot water is used for space heating and hot water consumption, whereas cold water is used for space cooling. Geothermal heat pumps influence thus both hot water and coldwater circuit demand of off-grid systems.
Geothermal heat pumps can operate in three modes:
- Simultaneous mode (heating and cooling)
- Heating mode
- Cooling mode

Figure 6. Scheme of the geothermal heat pump for the three operating modes(a) Simultaneous mode (cooling dominant), (b) Simultaneous mode (heating dominant), (c) Cooling mode, (d) Heating mode. Source: https://ietresearch.onlinelibrary.wiley.com/doi/epdf/10.1049/iet-rpg.2018.5505
Heat pumps are able to switch from one mode to the other, although the preferred mode is the simultaneous one. Switching between the modes is accomplished by means of controllable valves. Fig. 1 shows the different modes. In the simultaneous mode, the heat pump basically transfers heat from the cold water TESS to the hot water TESS. According to the demand, a simultaneous mode is differentiated into cooling-dominant and heating-dominant [7].
The geothermal well allows absorbing excess heat. For example, in the cooling-dominant mode in Fig., excess heat extracted from the cold water TESS is injected into the geothermal well if heat transfer is larger than the thermal demand of the hot water circuit. In the heating-dominant mode, by contrast, additional heat is extracted from the geothermal well to supply thermal heat demand. In the cooling mode, the heat pump transfers heat from the cold water TESS to the geothermal well (see Fig. c). A bypass valve allows for controlling the temperature of the brine. In the heating mode, the heat pump extracts heat from the geothermal pound and injects it into the hot water TESS. If the temperature of the hot water tank increases above a certain level (e.g. 70°C), the heat pump becomes unable to inject more heat into the hot water TESS.
4 References
[1] Refrigeration System. (n.d.). Applied Industrial Energy and Environmental Management, 355–393. doi:10.1002/9780470714379.ch11
[2] 2008 ASHRAE HVAC Systems and Equipment Handbook, chapter 39, “Cooling Towers.
[3] Day, A. R., Ratcliffe, M. S., & Shepherd, K. (2008). Heating systems, plant and control. John Wiley & Sons.
[4] Duffie & Beckman (1992) Solar Engineering of Thermal Processes, 2nd edn. John Wiley & Sons, New York.
[6] Webb, R.L. and W. Li. “Fouling in Enhanced Tubes Using Cooling Tower Water, Part I: Long-Term Fouling Data.” International Journal of Heat and Mass Transfer 43, no. 19 (October 2000): 3567-3578.
[7] IET Renew. Power Gener., 2019, Vol. 13 Iss. 6, pp. 961-972© The Institution of Engineering and Technology 2019.
[8] Bischi, A., Basile, M., Poli, D., Vallati, C., Miliani, F., Caposciutti, G., … & Desideri, U. (2021). Enabling low-voltage, peer-to-peer, quasi-real-time electricity markets through consortium blockchains. Applied Energy, 288, 116365.
[9] Vitalik Buterin et al. A next-generation smart contract and decentralised application platform. White paper, 3(37), 2014.
[10] Mishra, S., Crasta, C. J., Bordin, C., & Mateo‐Fornés, J. (2021). Smart contract formation enabling energy‐as‐a‐service in a virtual power plant. International Journal of Energy Research.
[11] Rodríguez, P. Standardization of Blockchain-based Applications in the Energy Sector (Doctoral dissertation, University of Freiburg).
[12] https://polkadotters.medium.com/energy-web-chain-time-to-disrupt-the-analog-energy-era-dfc73aa088ab
[13] Regulation No 1227/2011 of the European Parliament and of the Council of 25 October 2011 on wholesale energy market integrity and transparency (REMIT), available at https://www.emissionseuets.com/remitrecordswholesaleenergymarkettransactions