1. Carbon Dioxide Emissions Sources
CARBON DIOXIDE CAPTURING TECHNOLOGIES: Carbon dioxide (CO2) emissions are either natural or anthropic (due to human activity). Natural emissions come from natural wildfires, animal breathing, plants, aquatic microorganisms, the ground, or even volcanic origin. Anthropic emissions come from heating, vehicles, voluntary fire, and power generation stations of fossil fuels.
Since the Industrial Revolution, human sources of carbon dioxide emissions have been growing. Human activities such as burning oil, coal and gas and deforestation are the primary causes of the increased carbon dioxide concentrations in the atmosphere. Combustible fossil fuels such as coal, power plant gas, oil, vehicles and big industry are the largest sources of carbon dioxide. The production is from various items such as iron, steel, cement, natural gas, solid waste combustion, lime, ammonia, limestone, soda ash, aluminium, and petrochemicals. Carbon dioxide accounts for nearly 85 per cent of all emissions and is produced when natural gas, petroleum and coal are used. The major areas where these fuels are used include electricity generation, transportation, industry and residential and commercial buildings.
2. Consequences of CO2 on the Environment
CO2 is naturally present in the air, so it’s not harmful to a living organism. However, CO2 emissions are also accompanied by heavy metals, which are different contaminants. These, together, provoke deleterious effects on a living organism. This latest is sensitive to variations of the CO2 concentrations in the atmosphere. This emission has consequences for wildlife and plants.
- For birds and mammals, carbon can kill by asphyxiation at a certain level and time of exposition. Its chemical property, higher than oxygen, permits it to rapidly cross numerous types of biological membrane (including the central nervous system).
- In the oceans: Human carbon emissions also affect ocean circulation. They make oceans more acidic. Thus, numerous fish can wind up to the poles, where the water temperature changes less rapidly. Regarding ocean currents, they could slow down or even stop. The CO2 absorbed could be released and worsen climate change.
- For the plants: with a low dose, the CO2 can permit the growth of many vegetal species. After experience, this has been proven, but only to a certain level. When this level is overpassed, the growth of vegetal stabilize or reduce
- Climate change continues to play a significant role in the destruction of ecosystems. Global warming has led to increased temperatures, sea levels, and ocean acidity that disrupt an ecosystem’s natural balance.
3. What Is CO2 Capture and Storage
CO2 can be captured from large point sources, such as large fossil fuel or biomass electricity power plants, industries with major CO2 emissions, natural gas processing, synthetic fuel plants, and fossil fuel-based hydrogen production plants. Capture from the open atmosphere is also possible. Carbon capture has actually been in use for years. The oil and gas industries have used carbon capture for decades to enhance oil and gas recovery. Only recently have we started thinking about capturing carbon for environmental reasons.
Currently, most research focuses on carbon capture at fossil fuel-powered energy plants, the source of most man-made CO2 emissions. Many of these power plants rely on coal to create energy, and coal burning emits CO2 into the atmosphere. Some researchers envision a future where all new power plants employ carbon capture. There are three main steps to carbon capture and storage (CCS) –
- Trapping or Capturing
- Separating the CO2 from other gases,
- Transporting this captured CO2 to a storage location and storing that CO2 far away from the atmosphere (underground or deep in the ocean).
Carbon is taken from a power plant source in three basic ways — post-combustion, pre-combustion and oxyfuel combustion. A fossil fuel power plant generates power by burning fossil fuel (coal, oil or natural gas), which generates heat that turns into steam. That steam turns a turbine connected to an electricity generator. Let’s take a more detailed look at the trapping and separation process:
3.1 Post-Combustion Capturing
Post-combustion CO2 capture refers to the removal of CO2 from combustion flue gas before discharge to the atmosphere. It is referred to as “post-combustion capture” because the CO2 is the product of the combustion of the primary fuel, and the capture takes place after the combustion of that fuel.
With post-combustion carbon capture, the CO2 is grabbed after the fossil fuel is burned. This process is currently being used to remove CO2 from natural gas. The biggest benefit of using this process is that it allows us to retrofit older power plants by adding a “filter” that helps trap the CO2 as it travels up a chimney or smokestack. This filter is actually a solvent that absorbs carbon dioxide. The solvent can later be heated, releasing water vapour and leaving behind a concentrated stream of CO2. Post-combustion carbon capture can prevent 80 to 90 per cent of a power plant’s carbon emissions from entering the atmosphere, but the post-combustion process requires a lot of energy to compress the gas enough for transport.

Figure 1: Post-combustion CO2 capture
Process Description
In a typical fossil fuel-fired steam generating unit, fuel is burned with air in a boiler to produce steam that drives a turbine/generator to produce electricity. The burning of fossil fuels produces flue gases, which include CO2, water vapour, sulfur oxides (SOx), nitrogen oxides (NOx), hydrochloric acid (HCl) etc. In a post-combustion process, CO2 is separated and captured from the flue gases.
The CO2 capture process is located downstream of the conventional pollutant controls for removing Particulate matter and acid gases, so these components will not interfere with CO2 removal. Challenges to separating CO2 from steam-generating unit combustion flue gas include:
- The high volume of gas to be treated because the CO2 is dilute (13–15 volume per cent in coal-fired systems);
- The low pressure [15–25 pounds per square inch (psi)] of the flue gas;
- The large auxiliary power load to compress captured CO2 from near atmospheric pressure to pipeline pressure (about 2,200 psi).
3.2 Pre-combustion CO2 Capture
Pre-combustion CO2 capture, as its name implies, occurs before the process gas is combusted to generate steam at a power plant. CO2 is trapped before the fossil fuel is burned, which means it’s trapped before it’s diluted by other flue gases. Pre-combustion capture applies mainly to IGCC processes where fuel is converted into gaseous components by applying heat under pressure in the presence of steam and limited O2.

Figure 2: Pre-Combustion CO2 capture.
Process Description
Coal, oil or natural gas (usually coal or petroleum coke at electric utilities) is heated with water and oxygen in an oxygen-lean environment. Unlike a boiler, a gasifier carefully controls the amount of air or oxygen available inside it so that only a small portion of the fuel burns completely. This “partial oxidation” process provides heat to drive gasification reactions. Rather than burning, most of the fuel is chemically broken apart by the heat and pressure in the gasifier, setting into motion chemical reactions that produce syngas. The fuel (carbon), water and oxygen react to form primarily a mixture of hydrogen (H2) and carbon monoxide (CO) known as synthesis gas or “syngas” according to the following high-temperature reaction:
3C + H2O + O2 H2 + 3CO
Although syngas are predominantly H2 and CO, they can include other gaseous constituents (e.g., hydrogen sulfide (H2S), carbonyl sulfide (COS), and CO2) in varying compositions depending on fuel characteristics and the conditions in the gasifier. Most syngas streams are at a higher pressure and can contain higher concentrations of CO2 than conventional steam-generating units (especially if the syngas is shifted to enrich the CO2 concentration).
Pre-combustion capture systems have been used widely in industrial processes such as natural gas processing. The pre-combustion process is lower in cost, but it’s not a retrofit for older power plant generators. As with post-combustion, pre-combustion carbon capture can prevent 80 to 90 per cent of a power plant’s emissions from entering the atmosphere.
3.3 Oxy-combustion CO2 Capture
Oxy-combustion (or oxy-fuel) refers to replacing air in the boiler or gasifier with pure oxygen (O2). Purified O2 helps eliminate unwanted byproducts in the air and also increases the CO2 purity of the resulting syngas or flue stream, making CCS more effective. The oxygen required for this technique increases costs, but researchers are developing new techniques to bring this cost down. Oxy-fuel combustion can prevent 90 per cent of a power plant’s emissions from entering the atmosphere.
Oxy-combustion overcomes the technical challenge of low CO2 partial pressure normally encountered in conventional coal combustion flue gas by producing a highly concentrated CO2 stream. The CO2 is separated from water vapour by condensing the water through cooling and compression.
Oxy-combustion’s appeal is tempered by a few key challenges, including the capital cost and energy consumption for a cryogenic air separation unit (ASU), boiler air infiltration that dilutes the flue gas with N2, and excess O2 contained in the concentrated CO2 stream.
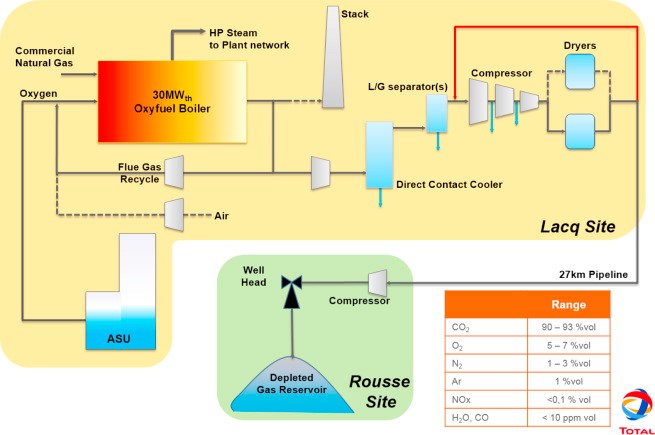
Figure 3: Oxy-combustion CO2 capture

4. Carbon Dioxide Capturing Technologies: CO2 Separation Techniques
Based on economic and environmental considerations, it is necessary to apply efficient and suitable technology for CO2 separation with low operating costs and energy consumption. Up to now, several gas separation technologies are being investigated for post-combustion capture, namely,
(a) Absorption,
(b) Adsorption,
(c) Cryogenic distillation, and
(d) Membrane separation
Although various new methods were suggested for CO2 separation, Granite and Brien reviewed some of the most novel methods for carbon dioxide separation from the flue and fuel gas streams, such as the use of electrochemical pumps and chemical looping for CO2 separation.

Figure 4: Separation Techniques
4.1 Gas Absorption Amines
Gas absorption processes using chemical solvents, such as amines, to separate CO2 from other gases have been used since the 1930s in the natural gas industry to produce food and chemical-grade CO2. As absorbents, the most commonly used are monoethanolamine (MEA), diethanolamine (DEA), methylodiethyloamine (MDEA) and triethanolamine (TEA). Low purchase costs and the availability of monoethanolamine (MEA) make it the most popular sorbent despite some obvious limitations.
The flue gas (containing CO2) is cooled (between 318 and 323 K), and fed to the absorption column (scrubber) where the solvent absorbs CO2. The CO2-rich solution is fed into a heater to increase the temperature of the solution, then to a stripper column to release the CO2. The released CO2 is compressed, and the regenerated absorbent solution is cooled and recycled to the absorber column. Solvent regeneration is responsible for much of the “energy penalty” of the CO2 capture system because the steam that could otherwise be used to generate electricity is instead used in the solvent regeneration process. Development of advanced solvents – those that are chemically stable, have high CO2 absorption capacities, and have low regeneration energy requirements – continues to be an active area of research.
Amines chemically react with CO2 via reversible reactions to form water-soluble compounds. Despite the low CO2 partial pressure in combustion flue gas, amines are capable of achieving high levels of CO2 capture due to fast kinetics and strong chemical reactions. However, the absorption capacity for commercially available amines is chemically limited, requiring two molecules of amine for each molecule of CO2. Besides, usable amine solution concentrations are typically limited by viscosity and corrosion. Therefore, current amine systems are only between 20 and 30 per cent amine, with the remaining being water. Although the water present in the solution helps control the solvent temperature during absorption, which is an exothermic reaction, the water also requires significant amounts of sensible heating and stripping energy upon CO2 regeneration.

Figure 5: Gas Absorption by MEA
4.1.1 Famous Solvents for Absorption
(1) Alkanolamines: Between various solvent groups, alkanol amines group is the most important and most used for CO2 A major problem in the usage of amines for CO2absorption is equipment corrosion; the corrosion rate of various amine solvents and the suggested corrosion rate could reduce in the following order:
Monoethanolamine (MEA) > 2-amino-2-methyl-1-propanol (AMP) > diethanolamine (DEA) > methyl diethanolamine (MDEA).
(2) Amino Acid: Amino acids have the same functional groups as alkanolamines and can be expected to behave similarly towards CO2 but do not deteriorate in the presence of oxygen. The most common amino acids used in gas-treating solvents are glycine, alanine, dimethylglycine, diethyl glycine, and several sterically hindered amino acids.
(3) Ammonia: Since ammonia is a toxic gas, preventing ammonia “slipping” into the atmosphere is necessary. Despite this disadvantage, the chilled ammonia process (CAP) was used for CO2 separation. In the CAP, CO2 is absorbed in an ammoniated solution at a lower absorption temperature (275–283 K) that reduced ammonia emissions from the CAP absorber. The ammonium carbonate solution resulted in approximately 38% carbon regeneration compared to the MEA solution.
4.2 Adsorption
Adsorption operation can reduce the energy and cost of the capture or separation of CO2 in post-combustion capture. To achieve this goal, it is necessary to find adsorbents with suitable properties. In general, CO2 adsorbent must have high selectivity and adsorption capacity and adequate adsorption/desorption kinetics, remain stable after several adsorption/desorption cycles and possess good thermal and mechanical stability. The method consists of condensation of vapour and gases on the surface of a solid adsorbent due to molecular forces. It uses the differences in sorption capacity of particular components of the separated gas mixture on a given adsorbent. The adsorbents used for CO2 separation are placed into two main categories: physical and chemical adsorbents.
A) Activated Carbon (AC):
It has several attractive characteristics, such as its high adsorption capacity, high hydrophobicity, low cost, and low energy requirement for regeneration. Activated carbons are inexpensive, insensitive to moisture, and easy to regenerate. These adsorbents have well-developed micro- and mesopore structures that are suitable for high CO2 adsorption capacity at ambient pressure.
Activated carbon may be produced from many raw materials such as coal, coke pitch, wood or biomass sources (e.g., sawdust, coconut shells, olive stones), often via two steps: carbonization and activation. Carbon molecular sieves (CMS), which are a sub-class of activated carbon with narrow pore size distribution (PSD), are kinetic-based adsorbents. They have been commercialized mainly for the separation of air and the production of high-purity N2. However, at low CO2 partial pressure, activated carbons exhibit lower adsorption capacity and selectivity than zeolites, mainly due to their less favourable adsorption isotherms. Despite the hydrophobic character of carbon-based adsorbents, their CO2 adsorption ability is adversely affected by the presence of water vapour.
B) Zeolites:
The most popular adsorbents are zeolite and carbon adsorbents, which constitute an adsorption bed when filled into the adsorption tower. For the process to be carried out continuously, at least two adsorption towers are required. In practice, multi-bed systems are used, which benefits the effectiveness of the process.
CO2/N2 selectivities of activated carbon are relatively low; zeolitic materials offer CO2/N2 selectivities 5–10 times greater than those of carbonaceous materials. The adsorption capacity and selectivity of zeolites are largely affected by their size, porous diameter, charge density, and chemical composition of cations in their porous structures. The average value of heat adsorption on zeolites is larger than that of activated carbon, confirming the mentioned affirmation. Moreover, activated carbon can be regenerated easily and completely. Also, its capacity did not decay after 10 consecutive process cycles.
C) Carbon Nanotubes (CNTs):
They are the most famous among nano-hollow structured materials, and their dimensions range from 1 to 10 nm in diameter and from 200 to 500 nm in length. Purified single-walled carbon nanotubes (SWNTs) adsorbed CO2 better than unpurified SWNTs. Also, multi-walled carbon nanotubes (MWNTs) showed stability for 20 adsorption and regeneration cycles.
D) MOFs and Zeolite-like MOFs:
Carbon dioxide adsorbs to a MOF Metal-Organic Framework through physisorption or chemisorption based on the MOF’s porosity and selectivity, leaving behind a Greenhouse gas-poor gas stream that is more environmentally friendly. The carbon dioxide is then stripped off the MOF using temperature swing adsorption (TSA) or pressure swing adsorption (PSA) to reuse the MOF. Adsorbents and absorbents require regeneration where the CO2 is removed from the sorbent or solution that collected it from the flue gas for the sorbent or solution to be reused.
Although an emerging class of porous materials, metal-organic frameworks (MOFs) have attracted a growing interest, motivating extensive studies on their CO2 adsorption properties, both theoretically and experimentally. MOFs are porous crystalline materials composed of self-assembled metallic species and organic linkers. Their pore size and shape can be easily tuned by changing either the organic ligands or the metallic clusters. They are typically rigid materials, but some of them exhibit structural flexibility upon adsorption and desorption of gases or liquids. The wide range of MOFs combined with their desirable properties, such as their remarkably high surface area and controlled pore size and shape, prompted extensive work on their absorptive properties, particularly for storing light gases (H2, CH4) and storing and separating CO2. Although most investigations on CO2 adsorption over MOFs used pure CO2 and CO2-containing mixtures, most measurements and simulations were carried out at high pressure and often at room or sub-ambient temperature.
4.2.1 Regeneration Cycles for CO2 Adsorption
Five different regeneration strategies were demonstrated in a single-bed CO2 adsorption unit: pressure swing adsorption (PSA), temperature swing adsorption (TSA), vacuum swing adsorption (VSA), electric swing adsorption (ESA), and a combination of vacuum and temperature swing adsorption (VTSA). The difference between these technologies is based on the strategy for the adsorbent regeneration after the adsorption step. In PSA applications, the pressure of the bed is reduced. VSA is preferred to the special PSA application where the desorption pressure is below atmospheric. In contrast, in TSA, the temperature is raised while pressure is maintained approximately constant, and in ESA, the solid is heated by the Joule effect.
4.3 Membrane Separation
The membrane separation method is a continuous, steady-state, clean and simple process, and ideal as an energy-saving method for CO2 recovery. Gas separation using membranes is a pressure-driven process. Due to the low pressure of flue gases, the driving force is too low for membrane processes in post-combustion (low pressure and low CO2 concentration). Membrane processes offer increased separation performances when CO2 concentration in the feed mixture increases.
Membrane separation processes have several advantages over other CO2 separation technologies. The required process equipment is simple, compact, relatively easy to operate and control, clear process and scale up.
The energy required for the recovery of CO2 by membrane processes depends on the target purity, flue gas composition, and membrane selectivity for CO2. However, membrane processes require too much energy for post-combustion CO2 capture; therefore, the low partial pressure of CO2 in the flue gas is a possible disadvantage for the application of membranes. Another disadvantage of the membrane process is that the membrane selectivity for separating CO2 is very low. The membrane process is not useful for high-flow rate applications.
Therefore, the useful membrane for post-combustion CO2 capture should have some specifications, such as:
- High CO2 permeability,
- High selectivity for CO2 separation from flue gases,
- High thermal and chemical stability,
- Resistant to participation,
- Resistant to ageing,
- Cost-effective,
- Low production cost for different membrane modules.
4.3.1 Hollow Fiber Membrane
Most industrially important membranes for gas separations are hollow fibre ones. Asymmetric hollow fibre membranes (such as polyvinylidene difluoride (PVDF)) with inner skinless structures are favourable for CO2 separation and absorption in the gas-liquid membrane by low mass-transfer resistance and high permeability. In addition, this process can achieve significantly high adsorption efficiencies due to the much larger surface area for the gas-liquid interface than conventional gas absorption processes.
4.4 Cryogenic Distillation
The Cryogenic method utilized low temperatures for condensation, separation, and purification of CO2 from flue gases (the freezing point of pure CO2 is 195.5 K at atmospheric pressure). Therefore, the components can be separated under the cryogenic separation process by a series of compression, cooling, and expansion steps. It enables direct production of liquid CO2 that can be stored or sequestered at high pressure via liquid pumping. The advantages of this technology can be summarized as follows:
(1) Liquid CO2 is directly produced, thus making it relatively easy to store or send for enhanced oil recovery.
(2) This technology is relatively straightforward, involving no solvents or other components.
(3) The cryogenic separation can be easily scaled up to industrial-scale utilization.
The major disadvantages of this process are the large amount of energy required to provide refrigeration and the CO2 solidification at a low temperature, which causes several operational problems. Therefore, more studies are required for reducing the cost of cryogenic separation A pilot-scale CO2 capture and compression unit (CO2 CCU) that can separate CO2 as liquid phase from the flue gas of oxy-fuel combustion. Their results showed that cryogenic is the most cost-effective when the feed gas is available at high pressure. Therefore, cryogenic is not suitable for post-combustion, but it is effective for separation streams with high CO2 concentrations, such as oxy-fuel combustion.
In a novel CO2 cryogenic liquefaction and separation system, two-stage compression, two-stage refrigeration, two-stage separation, and sufficient recovery of cryogenic energy were adopted. Furthermore, this CO2 cryogenic separation system is more suitable for gas mixtures with high initial pressure and high CO2 concentration.
5. Carbon Dioxide Capturing Technologies: Transportation
After capturing carbon dioxide, it is transported to a storage site. The current method of transporting CO2 is through a pipeline. Pipelines have been used for decades, and large volumes of gases, oil and water flow through pipelines daily.
A CO2 pipeline usually begins at the source of capture and travels directly to the storage site—although, in some cases, it might travel as far as it can in the pipe, then transition to a tanker or ship to finish its journey. It all depends on where the source, pipeline, and storage site are located. Both the public and private sectors can own pipelines.
Pipelines can transport CO2 in three states: gaseous, liquid and solid. Solid CO2 is commonly known as dry ice, and it’s not cost-effective to transport CO2 as a solid. Pipelines commonly transport carbon dioxide in its gaseous state. A compressor “pushes” the gas through the pipeline. Sometimes, a pipeline will have intermittent compressors to keep the gas moving. The CO2 must be clean (free of hydrogen sulfide) and dry. Otherwise, it can corrode a typical pipeline, which is made of carbon manganese steel. As of yet, there are no standards in place for “pipeline quality” carbon dioxide, but experts say that pipelines built from stainless steel would have a lowered risk of corrosion. This, however, may not be economical since we would have to build brand-new pipelines just for CO2.
As CO2 is odourless and colourless, though, adding an odour to the gas could help detect leaks. Regardless, experts recommend the construction of pipelines in low-population areas to minimize any impact. Pipeline costs fluctuate depending on the pipeline route (through heavily congested areas, mountains, offshore). Transporting CO2 as a liquid is possible, using ships or tanker trucks. Liquid CO2 requires low pressure and constant temperature, so cargo tanks must be pressurized and refrigerated.
6. Carbon Dioxide Applications
6.1 Multi-Industry Uses for CO2:
- Carbon dioxide, in solid and liquid form, is used for refrigeration and cooling. It is also used as an inert gas in chemical processes, in the storage of carbon powder, and in fire extinguishers.
6.2 Metals Industry:
- CO2 is used to manufacture casting moulds to enhance their hardness.
6.3 Oil Industry
- CO2 gas is used in enhanced oil recovery (EOR), a class of techniques for increasing the quantity of crude oil extracted from oil fields. It is injected under high pressure into an oil reservoir, pushing the oil through pipes and up to the ground’s surface. CO2 gas injection aids oil recovery and reduces the viscosity of recovered oil.
6.4 Manufacturing and Construction Uses:
- CO2 is used on a large scale as a shielding gas in MIG/MAG welding, where the gas protects the weld puddle against oxidation by the surrounding air. A mixture of argon and carbon dioxide is commonly used today to achieve a higher welding rate and reduce the need for post-weld treatment.
- Dry ice pellets are used to replace sandblasting when removing paint from surfaces. This reduces the cost of disposal and cleanup.
6.5 Chemicals, Pharmaceuticals and Petroleum Industry Uses:
- Large quantities are used as raw material in the chemical process industry, especially for methanol and urea production.
6.6 Rubber and Plastics Industry Uses:
- Flash is removed from rubber objects by tumbling them with crushed dry ice in a rotating drum.
6.7 Food and Beverages Use for Carbon Dioxide:
- Liquid or solid carbon dioxide is used for quick freezing, surface freezing, chilling and refrigeration in the transport of foods. In cryogenic tunnels and spiral freezers, high-pressure liquid CO2 is injected through nozzles that convert it to a mixture of CO2 gas and dry ice “snow” covering the food product’s surface. Refrigeration is transferred to the product as it sublimates (goes directly from solid to gas states).
- CO2 gas is used to carbonate soft drinks, beers and wine, preventing fungal and bacterial growth.
- Liquid CO2 is a good solvent for many organic compounds. It is used to decaffeinate coffee.
- It is used as an inert “blanket,” a product-dispensing propellant, an extraction agent, and to displace air during canning.
- Producers of flavours and fragrances use supercritical CO2 extraction coupled with a fractional separation technique to separate and purify volatile flavour and fragrance concentrate.
- Cold sterilization can be carried out with a mixture of 90% CO2 and 10% ethylene oxide. The carbon dioxide stabilizes the ethylene oxide and reduces the risk of explosion.
6.8 Health Care Uses:
- CO2 is used as an additive to oxygen for medical use as a respiration stimulant.
6.9 Environmental Uses:
- Used as a propellant in aerosol cans, it replaces more environmentally troublesome alternatives.
- Using dry ice pellets instead of sandblasting to remove paint from surfaces greatly reduces residue disposal problems.
- It is used to neutralize alkaline water.
7. References
[1] D.J. Hofmann, J.H. Butler, P.P. Tans, A new look at atmospheric carbon dioxide, Atmos. Environ. 43 (2009) 2084–2086.
[2] Kim Y., Lim J., Jeong S., Yoon Y., Bae S., Nam S., 2013. Comparison of carbon dioxide absorption in aqueous MEA, DEA, TEA, and AMP solutions. Bulletin of the Korean Chemical Society 34 (3), 783-787.
[3] Ben-Mansour R., Habib M., Bamidele O.E., Basha M., Qasem N., Peedikakkal A., Laoui T., Ali M., 2016. Carbon capture by physical adsorption: materials, experimental investigations, numerical modelling, and simulations – a review. Applied Energy 161, 225-255.
[4] J.P. Ciferno, T.E. Fout, A.P. Jones, J.T. Murphy, Capturing carbon from existing coal-fired power plant, Chemical Engineering Progress (April 2009) 33.
[5] J.E. Koresh, A. Soffer, The carbon molecular-sieve membranes—General properties and the permeability of CH4/H2 mixture, Separation Science and Technology 22 (1987) 973.
[6] O.M.Yaghi, M. O’Keeffe, M.W. Ockwing, M. Chae, M. Eddaoudi, J., Reticular synthesis and the design of new materials, Nature 423 (2003) 705–714.
[7] P.L. Llewellyn, S. Bourrelly, C. Serre, A. Vimont, M. Datura, L. Hamon, G. De Wereld, J.S. Chang, D.Y. Hong, Y.K. Hwang, S.H. Jhung, G. Ferey, High uptakes of CO2 and CH4 in mesoporous metal-organic frameworks MIL-100 and MIL101, Langmuir 24 (2008) 7245–7754.
[8] A.R. Millward, O.M. Yaghi, Metal-organic frameworks with exceptionally high capacity for storage of carbon dioxide at room temperature, J. Am. Chem. Soc. 127 (2005) 17998–17999.
[9] K. E. Zanganeh, A. Shaheen, and C. Salvador, “CO2 capture and development of an advanced pilot-scale cryogenic separation and compression unit,” Energy Procedia, vol. 1, pp. 247–252, 2009.
[10] H. Yang, Z. Xu, M. Fan et al., “Progress in carbon dioxide separation and capture: a review,” Journal of Environmental Sciences, vol. 20, no. 1, pp. 14–27, 2008.