This article aims to provide an overview of current and emerging hydrogen production technologies, which serve as a critical link in the hydrogen supply chain.
Hydrogen can be generated in various ways using traditional sources such as fossil fuels and renewable energy sources such as biomass, solar- and wind power (Nikolaidis and Poullikkas 2017).
1 Overview of hydrogen supply chain
The supply chain for hydrogen comprises the processes necessary to produce, store, distribute, and utilise hydrogen.
Since hydrogen only exists on earth as part of a compound, it must be synthesised in specific processes for pure hydrogen to be used as a material or energy source. Hydrogen can be produced either from fossil fuels or renewable sources via various technical processes. The most important primary energy source for hydrogen production today is natural gas, with steam reforming being the most important hydrogen production method. Only small quantities of hydrogen have been produced from renewable energy, but it is expected to rise in the future. Electrolysis from renewable electricity can offer tremendous potential for the future since it produces the lowest greenhouse gas emissions.
A significant advantage of hydrogen is that it can be stored in large amounts for extended periods. Hydrogen has a very low volumetric energy density, which means that it has to be compressed for storage and transportation purposes. Liquefying hydrogen allows for a higher storage density. The most common commercial storage method – particularly for end-users – is hydrogen as a compressed gas.
At present, hydrogen is generally transported by road or rail in pressurised gas containers, and in some cases, also in cryogenic liquid tanks. Moreover, hydrogen pipeline networks are available in some locations. Liquid hydrogen is best for long-distance transport, compressed gaseous hydrogen is suitable for shorter distances in smaller quantities, while pipelines are advantageous for large volumes.
Hydrogen is a highly versatile basic chemical with two main areas of use: material applications and energy applications. The most important industrial applications are ammonia synthesis, which is primarily used to produce nitrogenous fertilisers and methanol synthesis. For energy applications, fuel cells have become the main focus of hydrogen usage. Fuel cells offer much higher electrical efficiency and overall efficiency than heat engines.
Each process in the hydrogen supply chain plays a significant role and will be addressed in greater detail, emphasising hydrogen production processes.
2 Hydrogen production processes
Hydrogen (H2) is not readily available in nature since it only exists in chemically bound form. Therefore, hydrogen has to be produced through specific processes to be used for chemical or energy purposes (Adolf, Balzer et al. 2017). The major problem in utilising hydrogen gas as a fuel is its unavailability in nature and the need for inexpensive production methods (Kapdan and Kargi 2006).
A wide variety of processes are available for hydrogen production, divided into two categories based on the raw materials used: traditional and renewable technologies. Each category can further be divided into the different hydrogen production methods, as illustrated in Figure 2.

Figure 2: Hydrogen production methods (Nikolaidis and Poullikkas 2017)
The methods of hydrocarbon reforming and pyrolysis are included in the first group, which processes fossil fuels. Steam reforming, partial oxidation, and autothermal steam reforming are the chemical techniques used in the hydrocarbon reforming process. The methods that generate hydrogen from renewable resources, such as biomass or water, fall into the second group.
The processes that use biomass as a feedstock can be divided into two categories: thermochemical and biological processes. Pyrolysis, gasification, combustion, and liquefaction are the most common thermochemical processes. While bio-photolysis, dark fermentation and photo-fermentation are the most common biological processes. The methods that generate H2 from water-splitting processes use water as the only material input and include electrolysis, thermolysis, and photo-electrolysis (photolysis) (Nikolaidis and Poullikkas 2017).
2.1 H2 production from fossil fuels
Fuel processing technologies convert a hydrogen-containing material such as gasoline, ammonia, or methanol into a hydrogen-rich stream. The majority of hydrocarbon fuels contain sulphur, which poisons the fuel processing catalyst. This is probably the most challenging aspect of reforming (Holladay, Hu et al. 2009). Hydrocarbon reforming and -pyrolysis are the most developed and commonly used methods, satisfying almost all hydrogen demand (Nikolaidis and Poullikkas 2017).
2.1.1 Hydrocarbon reforming
Hydrocarbon reforming, by definition, is the method of converting hydrocarbon fuel into hydrogen using reforming techniques. The reforming reaction occurs at high temperatures (approximately 700°C to 900°C), and the conversion is assisted by a catalyst (Adolf, Balzer et al. 2017). Reforming requires the addition of an oxidant, which provides the necessary oxygen. When a hydrocarbon reacts with steam (water), it undergoes an endothermic reaction known as steam reforming. And when the hydrocarbon reacts with oxygen, it undergoes an exothermic reaction known as partial oxidation. When these two reactions are combined, hydrogen reacts with a mixture of air and water vapour known as an autothermal reaction (Chen, Lee et al. 2008). The ratio of the two oxidants is adjusted so that no heat needs to be introduced or discharged, therefore being an isothermal reaction (Adolf, Balzer et al. 2017).
2.1.1.1 Steam reforming (SR)
Steam reforming process entails a catalytic conversion of hydrocarbon and steam to produce hydrogen and carbon oxides. Steam reforming’s key steps include converting raw materials into syngas, a water-gas-shift (WGS) reaction and methanation or gas purification. The raw materials for steam reforming are primarily methane and water; in principle, however, other light hydrocarbons such as liquefied petroleum gas or naphtha can also be used. If the feedstock contains organic sulphur compounds, a desulphurisation step is performed before the reforming step to avoid poisoning the catalyst (Balthasar 1984).
The reforming reaction’s operation parameters are chosen at high temperatures, pressures up to 3.5 MPa, and steam-to-carbon rations of 3.5 to achieve an H2 product with the desired purity while preventing coking formation on the catalyst surface.
Steam methane reforming is the most common and developed method used for large-scale hydrogen production and will describe the steam reforming process’s steps. The process starts where methane and water react in the reformer to form synthesis gas, consisting predominately of hydrogen and carbon oxide (CO). The gas mixture is passed through a heat recovery step and is fed into a WGS reactor where the CO reacts with steam to produce additional H2. Suitable catalysts can help achieve a higher yield of hydrogen (Adolf, Balzer et al. 2017). In the next step, the CO content is further reduced through CO methanation and selective CO oxidation. The purity of the product gas is further increased by subsequent CO2 washing and other purification steps, leaving H2 with a higher purity of nearly 100%. The CO2 emissions can be strongly reduced by CO2 capture and storage (CCS) technologies (Nikolaidis and Poullikkas 2017).
2.1.1.2 Partial oxidation (POX)
Partial oxidation is the exothermic conversion of mainly heavy hydrocarbons (such as heavy fuel oil or coal) with oxygen (O2) to produce hydrogen and carbon oxides. Thermal partial oxidation occurs at high pressures and temperatures ranging from 1 250°C to 1 400°C. Other than the partial combustion of the raw material, no external heat source is needed since heat is emitted (Adolf, Balzer et al. 2017).
After the sulphur is removed, pure O2 is used to oxidise the hydrocarbon feedstock partially, and the resulting syngas is processed in the same way as the product gas of the steam reforming process. In this process, the longer the chain length of the hydrocarbon used, the lower the hydrogen yield.
Due to the high energy cost of the oxygen plant and the additional costs of desulphurisation steps, such a plant is highly capital intensive (Balthasar 1984). Using O2 instead of air essentially removes nitrogen in the WGS reaction, resulting in lower energy consumption since separation and purification processes will not be necessary.
Overall, partial oxidation is less efficient than steam reforming. Still, it has the advantage of being able to convert a wider variety of raw materials, rather than relying solely on light hydrocarbons (Zakkour and Cook 2010).
2.1.1.3 Autothermal reforming (ATR)
Autothermal reforming is a combination of SR and POX. The reformer is injected with steam and oxygen or air, allowing for the reforming and oxidation reactions simultaneously (Chen, Lee et al. 2008). The ATR method uses the endothermic steam reforming step to increase the hydrogen production and the exothermic partial oxidation step to provide the required process heat (Adolf, Balzer et al. 2017). The ATR process, therefore, does not need an external heat source for the reactor. However, to feed pure oxygen to the reactor and prevent the product gas from being diluted with nitrogen, an expensive and complex oxygen separation unit is required (Holladay, Hu et al. 2009).
2.1.2 Hydrocarbon pyrolysis
Hydrocarbon (CHs) pyrolysis is a well-known process in which the only hydrogen source is the hydrocarbon itself, which undergoes thermal decomposition. The synthesis of elemental carbon and hydrogen is achieved by thermo-catalytic decomposition of light liquid hydrocarbons (the boiling point between 50 and 200 °C). In contrast, hydrogen is produced in a two-step scheme, namely hydrogasification and methane cracking, in the case of heavy residual fractions (boiling point greater than 350 °C) (Nikolaidis and Poullikkas 2017).
WGS and CO2 removal steps are not used in pyrolysis. Since CCS is an energy-intensive stage, it would be more environmentally sustainable to produce hydrogen and carbon through catalytic dissociation of natural gas rather than hydrogen production via SR combined with CO2 sequestration (Muradov and Veziroǧlu 2005).
2.2 H2 production from renewable sources
The persistent combustion of fossil fuels releases greenhouse gases (GHG) into the atmosphere, posing a significant threat to the global environment and consequent climate change. The key drivers of renewable hydrogen technology development are climate change and the depletion of fossil fuels. Future energy sources must meet the criteria of being carbon-free and sustainable to combat climate change in the long run (Lund 2007).
Hydrogen is widely recognised as an environmentally sustainable secondary source of renewable energy that can replace fossil fuels since it is carbon-free and has the highest energy content of any known fuel (Momirlan and Veziroglu 2005).
Although hydrocarbons are currently the most common feedstock for H2 production, the need to integrate renewable technologies will become inevitable. As the use of fossil fuels decreases and the greenhouse effect attracts more attention, it is predicted that renewable technologies will become more prevalent shortly, ultimately replacing traditional technologies (Lund 2007, Ćosić, Krajačić et al. 2012).
There are many processes to produce H2 from renewable resources, including biomass-based technologies and water splitting approaches.
2.2.1 Biomass process
Biomass is a renewable source of primary energy derived from plant and animal material such as crop residues, agricultural wastes, wood from forests and forest residues, industrial residues, municipal solid waste and many more (Steinberg 2004). Biomass is most likely to become the green organic alternative for petroleum soon (Holladay, Hu et al. 2009).
On a global scale, the production of hydrogen from biomass has so far been negligible. However, in the long run, this manufacturing alternative could play a role in low-CO2 hydrogen production – given that the biomass used meets the sustainability requirements and sufficient quantities are available (Adolf, Balzer et al. 2017).
There are two modes for producing H2 from biomass, namely thermochemical and biochemical methods. Biological processes are more environmentally friendly and energy-efficient since they operate under mild conditions, but they produce low rates and yields of hydrogen depending on the raw materials used (Balat and Kırtay 2010). On the other hand, thermochemical methods are much faster and produce a higher stoichiometric yield of hydrogen, with gasification being a promising alternative from both an economic and environmental standpoint (Demirbaş 2001, Parthasarathy and Narayanan 2014).
2.2.1.1 Biological processes
Over the past few years, research into biological hydrogen production has increased significantly due to increased attention to sustainable development and waste minimisation. Most biological processes operate at ambient temperature and pressure, thus less energy-intensive. Furthermore, they use inexhaustible renewable energy resources and contribute to waste recycling by using various waste materials as feedstock (Das and Veziroǧlu 2001).
Converting sugar, starch, and lignocellulose from biomass into hydrogen can be achieved in various ways. The most suitable methods are dark fermentation using heterotrophic bacteria, photo-fermentation using photosynthetic bacteria, and bio-photolytic splitting of water using green algae or cyanobacteria (blue-green algae).
Bio-photolysis uses the same photosynthesis principles found in plants and algae but adapts them for hydrogen gas generation. On the contrary, algae contain hydrogen-producing enzymes and can produce hydrogen under certain conditions (Das and Veziroǧlu 2001). Algae is used to split water molecules into hydrogen ions and oxygen. When green algae is used, it is known as direct bio-photolysis, and when blue-green algae is used, it is known as indirect bio-photolysis (Nikolaidis and Poullikkas 2017).
Fermentations occur with or without oxygen and perform microbial transformations of organic feed materials producing alcohols, acetone and H2 in minimal amounts and CO2. These methods are an appealing approach for bio-hydrogen production since they provide low-cost energy generation while treating waste (Balthasar 1984).
Dark fermentation uses anaerobic bacteria to ferment carbohydrate-rich substrates under anoxic (no oxygen), dark conditions. Glucose is usually the preferred source, but starch-containing materials or cellulose can also be used (Kapdan and Kargi 2006). Glucose is relatively expensive and is not readily available in high quantities but can be obtained from agriculture waste. Another constraint is that the hydrogen must be removed as it is generated since a pressure increase will decrease H2 production (Holladay, Hu et al. 2009). However, dark fermentation is accomplished by a relatively simple process that does not require light sources. As a result, a large amount of land is not needed, and hydrogen can be generated at any time of day or night from a wide range of potentially usable substrates, including refuse and waste products (Das and Veziroǧlu 2001).
Photo-fermentation is the final biochemical process, which operates in nitrogen-deficient conditions using solar energy and organic acids. Some photo-synthetic bacteria can transform organic acids (acetic, lactic, and butyric) into H2 and CO2 due to the presence of nitrogenase (Das and Veziroglu 2008). Increasing light intensity has a stimulatory effect on H2 yield and production rate but an adverse effect on the light conversion efficiency. Although the production of hydrogen is typically higher under illuminated conditions than in the dark; the poor efficiency of solar energy conversion, the need for elaborate anaerobic photo-bioreactors covering large areas (Ni, Leung et al. 2006), and the scarcity of organic acids (Holladay, Hu et al. 2009) are the main obstacles preventing this method from competing with the process mentioned above.
Common to all biochemical methods is that they exist only on a laboratory scale and are performed in tiny quantities. Market maturity is not yet in sight since conversion rates and hydrogen yields are still well below a marketable level, requiring significant increases.
All biochemical hydrogen processing methods, except bio-photolysis, require large amounts of biomass. Since biomass is a renewable raw material whose capacity and availability are restricted by various requirements, such as sustainability and competing uses, it could result in large-scale production restrictions (Adolf, Balzer et al. 2017).
2.2.1.2 Thermochemical processes
Thermochemical technology mainly involves pyrolysis and gasification of solid or liquid biomass to form synthesis gas. The synthesis gas can be further processed to produce hydrogen through steam reforming and WGS reaction (Nikolaidis and Poullikkas 2017). Combustion and liquefaction are two less desirable approaches that will not be explored in addition to these techniques.
Biomass pyrolysis produces liquid oils, solid charcoal, and gaseous compounds by heating biomass at temperatures between 650 and 800 °C and pressures between 0.1 and 0.5 MPa (Demirbaş 2001). The process occurs in the total absence of oxygen, except in cases where partial combustion is allowed to provide the thermal energy needed for the process (Parthasarathy and Narayanan 2014). Methane and other hydrocarbon gases can be steam reformed, and the WGS reaction can be used to produce even more hydrogen. After CO is converted into CO2, the desired purified H2 is obtained by pressure swing adsorption (PSA). The yield of hydrogen production from biomass pyrolysis depends on the type of feedstock, the type of catalyst used, the temperature and the residence time (Demirbaş 2001).
Biomass gasification is the thermochemical conversion of biomass into a gaseous fuel (syngas) when it reacts with air or steam. The process takes place at temperatures ranging from 500 to 1400 °C and operating pressures ranging from atmospheric to 33 bar depending on the plant scale and the final application of the produced syngas. The type of reactors used is dependent on the flow and velocity of the gasifying agent (Iribarren, Susmozas et al. 2014). The three main types of reactors used for biomass gasification are fixed bed, fluidised bed, and indirect gasifiers.
The syngas is treated similarly to the product gas of the pyrolysis process. However, the key parameters influencing hydrogen yield are biomass type, particle size, temperature, steam-to-biomass ratio, and catalyst type (Fremaux, Beheshti et al. 2015). The hydrogen yield is much higher for steam gasification than fast pyrolysis, and the overall efficiency can reach up to 52%, making it a viable source of renewable hydrogen (Parthasarathy and Narayanan 2014).
2.2.2 Water splitting
Water is one of the most abundant and inexhaustible raw materials on earth and can be used for H2 production through water-splitting processes such as electrolysis, thermolysis and photo-electrolysis (Steinfeld 2005). Provided that the required energy input is supplied from renewable energy sources, the produced hydrogen will be the cleanest energy carrier in use.
2.2.2.1 Electrolysis
Electrolysis is an established and well-known method, constituting the most effective technique for water splitting. The electrolyser consists of a DC source and two noble-metal-coated electrodes, which are separated by an electrolyte. The reaction is very endothermic. So, the required energy input is provided by electricity (Rossmeisl, Logadottir et al. 2005). Generally, when an electrical current is applied to water, it splits, with hydrogen produced at the cathode and oxygen released at the anode (Levene, Mann et al. 2007). The efficiency of electrolysis is determined by the amount of electricity used to produce an amount of hydrogen. The efficiency of water electrolysers is currently in the range of 60 to 80 %, depending on its method (Adolf, Balzer et al. 2017).
Alkaline electrolysis cells (AEC), polymer electrolyte membrane (PEM), and solid oxide electrolysis cells (SOEC) are the most developed and widely used electrolysis technologies to date. In a PEM electrolyser, water is introduced at the anode, where it splits into protons (hydrogen ions H+) which then pass through the membrane to the cathode and form H2 and O2 that remains back with water. In an AEC and SOEC, water is introduced at the cathode where it splits into H2 (which is isolated from water in an external separation unit) and hydroxide ions (OH–), which then pass through the aqueous electrolyte to the anode, where it is converted to O2 (Rossmeisl, Logadottir et al. 2005).
Although electrolysis can generate extremely pure hydrogen from water, electrolysers’ high electricity consumption prevents the production cost from competing with other large-scale technologies (Dönitz and Erdle 1985). However, if the electrical energy is provided by renewable sources such as hydro-, wind-, and solar power, the H2 produced is the cleanest energy carrier. It can store excess electricity and improve the plant load factor and efficiency on a small scale (Liu, Zhu et al. 2014, Parthasarathy and Narayanan 2014). In this way, water electrolysis offers a more sustainable and cost-effective option.
2.2.2.2 Thermolysis
Thermolysis is the process of heating water to a high temperature until it decomposes into hydrogen and oxygen. Despite its simplicity, water does not decompose until it reaches a very high temperature, usually over 2500 °C (Funk 2001). Since such high primary energy expenditures could not be met with renewable heat sources, multiple thermochemical water-splitting cycles have been proposed to lower the temperature and increase the overall efficiency. Thermochemical cycles consist of a series of chemical reactions at various temperatures. They are one of the most promising ways through which heat is converted into chemical energy in the form of hydrogen (McKendry 2002).
2.2.2.3 Photolysis
In general, photolysis occurs when visible light energy is absorbed with the aid of photo-catalysts and is then used to decompose water into H2 and O2. Semiconducting materials absorb sunlight, and the water splitting mechanism is similar to that of electrolysis (Kothari, Buddhi et al. 2008).
2.3 Overall comparison
The three hydrocarbon reforming methods, which include steam reforming, partial oxidation, and autothermal reforming, constitute a mature and highly developed hydrogen production technique through infrastructure that already exists. Compared to renewable methods, these methods have an efficiency of up to 85%, making them the most viable and advantageous approach. On the contrary, the reliance on fossil fuels, together with the CO2 by-product emitted into the atmosphere during the reforming process, are the major constraints that have prompted most studies to look into alternative, sustainable methods. Since fossil fuels are currently used as both reactants and fuel for the process, these methods’ cost is very reliant on their price and availability (Nikolaidis and Poullikkas 2017).
Table 1 compares the different hydrogen production technologies according to their energy conversion efficiency and significant advantages and disadvantages.
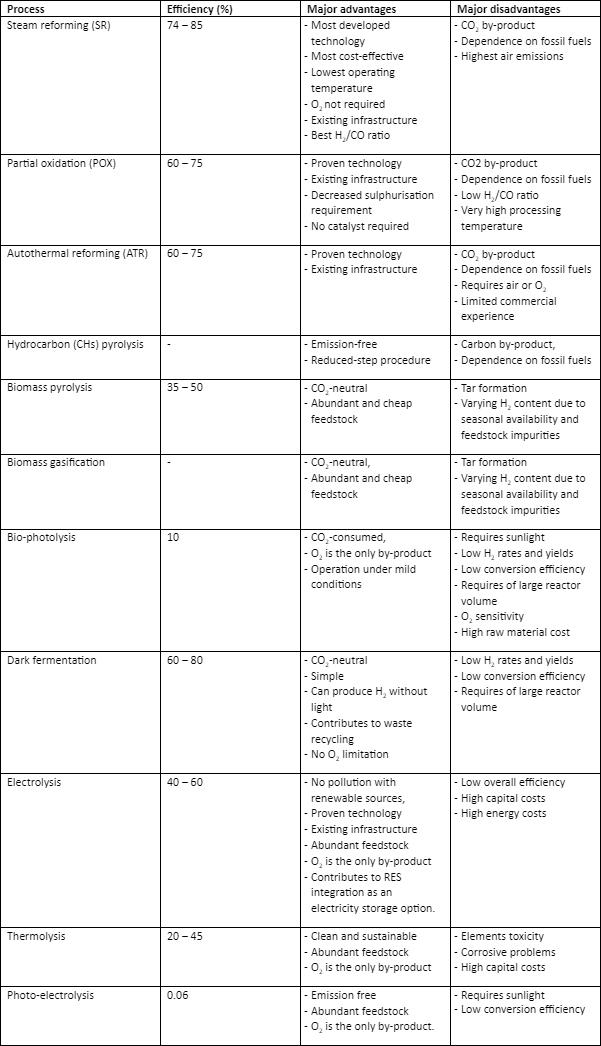
Table 1: Comparison of the different hydrogen production processes (Holladay, Hu et al. 2009, Nikolaidis and Poullikkas 2017)
3 Storage and transportation
3.1 Storage
The energy content of an energy carrier has a significant impact on how it is stored. The calorific value of an energy source determines its energy content. The calorific value is a precise measurement dependent on the mass of the energy source. The mass-based calorific value can also be translated into a volumetric energy density using the density (kg/l). Hydrogen has the largest gravimetric energy density of any energy carrier. However, hydrogen’s volumetric energy density is comparatively low (Adolf, Balzer et al. 2017).
At ambient temperatures and atmospheric pressure, 1 kg of hydrogen gas occupies a volume of 11 m3. With such a low density of 0.09 kg/m3, hydrogen storage has been one of the main impediments to its widespread adoption (Züttel 2003). As a result, hydrogen density must be increased significantly for storage purposes to make it practical to handle.
Physical storage methods are the most mature and the most frequently used. These methods include high-pressure storage, cooled or cryogenic hydrogen storage and a combination of the two. Hydrogen is exceptionally diffusive and can pass through a porous material or even metals (Wiberg, Wiberg et al. 2007). Therefore, high-pressure storage of hydrogen requires a special solid steel or steel composite pressure vessel with coatings or diffusion barrier layers to prevent any stored hydrogen losses. Because hydrogen heats up when compressed, it is often treated at high pressures or the hydrogen gas is precooled. Compressed gaseous hydrogen (CGH2) stored at pressures between 350 bar and 700 bar has become the norm for use in the mobility sector (Adolf, Balzer et al. 2017).
Hydrogen has to be cooled down to a very low temperature for cold- or cryogenic hydrogen to be stored in the liquid state. As an energy carrier, liquefied hydrogen (LH2) has a higher energy density than gaseous hydrogen. LH2 requires liquefaction at -253 °C, which involves a complex technical plant and an additional economic cost (Adolf, Balzer et al. 2017).
These two storage methods can be combined to create cryo-compressed hydrogen, where hydrogen is cooled to a temperature near its critical temperature and then compressed (Ahluwalia, Hua et al. 2010). The advantage of cold or cryogenic compression is that it has a higher energy density than compressed hydrogen. Cooling, on the other hand, necessitates an additional energy supply.
3.2 Transportation
The main commercial transport option for CGH2 is either by road, rail or pipeline, while LH2 is mainly transported by road or rail in insulated cryogenic tanks (Adolf, Balzer et al. 2017). The low density of hydrogen also impacts its transport since large tanks are required to transport a sufficient amount of hydrogen. Since LH2 has a higher density, more hydrogen can be transported in the liquid state. This way of hydrogen transport is usually more cost-effective.
A pipeline network would be the best for widespread and large-scale usage of hydrogen as an energy source. However, pipelines necessitate a sizeable initial expenditure that could pay off, but only with correspondingly large volumes of hydrogen. In 2016 there was more than 4 500 km of hydrogen pipelines in the world (Adolf, Balzer et al. 2017).
4 Hydrogen markets
There are many applications for hydrogen. It has two main areas of use: material applications and energy applications. Material applications involve using large quantities of hydrogen for chemical product synthesis, especially to form ammonia and methanol. Hydrogen is also used at refineries for the processing of intermediate oil products.
The physical and chemical properties of substances affect their application and utility and how they are handled (Adolf, Balzer et al. 2017). Hydrogen’s chemical properties make it excellent combustion and automotive fuel. The flammability of hydrogen is its most distinguishing chemical property. In comparison to other fuels, hydrogen is explosive over a vast concentration range. The lower and upper explosive limits of hydrogen are correspondingly large: the lower limit is at a concentration of 4 vol%, and the upper limit is at 77 vol%. Figure 1 shows how current liquid and gaseous fuels have much lower ignition ranges when compared to hydrogen. The combustion properties of hydrogen make it a fascinating combustion fuel. The broad ignition limits of hydrogen would allow for lean air/hydrogen gas mixtures if used in internal combustion engines.

Figure 1: Ignition range of fuels (Wiberg, Wiberg et al. 2007).
In terms of energy applications, hydrogen is, above all, a secondary energy source and chemical energy store since it is a clean and potent fuel with high energy content and attractive combustion properties. Hydrogen has been used for space travel since the 1950s, both as fuel and as an on-board power source for spaceships. The energy that hydrogen contains can also be used either in thermally operating heat engines or in fuel cells. Due to recent advances in fuel cell technology and the technical criteria that apply to hydrogen-powered heat engines, hydrogen as a fuel is now almost exclusively based on the fuel cell.
In fuel cells, the energy contained in hydrogen is converted into electrical and heat energy. The energy conversion determines the maximum efficiency of a fuel cell, which can achieve a cell efficiency of over 80%.
Unlike heat engines, a fuel cell can convert chemically bound energy directly into electrical energy, bypassing the need for a thermal power mechanism. The Carnot efficiency denotes the optimum efficiency of heat engines: the ratio of the (upper) combustion temperature to the (lower) incoming air temperature. Whether powered by gasoline or diesel, real heat engines remain well below theoretical Carnot efficiencies and emit both air pollution and greenhouse gasses.
Compared to traditional internal combustion engines, the most significant benefit of hydrogen and fuel cells in road transport is the higher efficiency of the energy converter, zero-pollution operation, and functionality.
5 References
Adolf, J., et al. (2017). “Energy of the future?: Sustainable mobility through fuel cells and H2; Shell hydrogen study.”
Ahluwalia, R., et al. (2010). “Technical assessment of cryo-compressed hydrogen storage tank systems for automotive applications.” International journal of hydrogen energy 35(9): 4171-4184.
Balat, H. and E. Kırtay (2010). “Hydrogen from biomass–present scenario and future prospects.” International journal of hydrogen energy 35(14): 7416-7426.
Balthasar, W. (1984). “Hydrogen production and technology: today, tomorrow and beyond.” International journal of hydrogen energy 9(8): 649-668.
Chen, H. L., et al. (2008). “Review of plasma catalysis on hydrocarbon reforming for hydrogen production—interaction, integration, and prospects.” Applied Catalysis B: Environmental 85(1-2): 1-9.
Ćosić, B., et al. (2012). “A 100% renewable energy system in the year 2050: The case of Macedonia.” Energy 48(1): 80-87.
Das, D. and T. N. Veziroglu (2008). “Advances in biological hydrogen production processes.” International journal of hydrogen energy 33(21): 6046-6057.
Das, D. and T. N. Veziroǧlu (2001). “Hydrogen production by biological processes: a survey of literature.” International journal of hydrogen energy 26(1): 13-28.
Demirbaş, A. (2001). “Biomass resource facilities and biomass conversion processing for fuels and chemicals.” Energy conversion and Management 42(11): 1357-1378.
Demirbaş, A. (2001). “Yields of hydrogen-rich gaseous products via pyrolysis from selected biomass samples.” Fuel 80(13): 1885-1891.
Dönitz, W. and E. Erdle (1985). “High-temperature electrolysis of water vapor—status of development and perspectives for application.” International journal of hydrogen energy 10(5): 291-295.
Fremaux, S., et al. (2015). “An experimental study on hydrogen-rich gas production via steam gasification of biomass in a research-scale fluidised bed.” Energy conversion and Management 91: 427-432.
Funk, J. E. (2001). “Thermochemical hydrogen production: past and present.” International journal of hydrogen energy 26(3): 185-190.
Holladay, J. D., et al. (2009). “An overview of hydrogen production technologies.” Catalysis today 139(4): 244-260.
Iribarren, D., et al. (2014). “Environmental and exergetic evaluation of hydrogen production via lignocellulosic biomass gasification.” Journal of cleaner production 69: 165-175.
Kapdan, I. K. and F. Kargi (2006). “Bio-hydrogen production from waste materials.” Enzyme and microbial technology 38(5): 569-582.
Kothari, R., et al. (2008). “Comparison of environmental and economic aspects of various hydrogen production methods.” Renewable and sustainable energy reviews 12(2): 553-563.
Levene, J. I., et al. (2007). “An analysis of hydrogen production from renewable electricity sources.” Solar energy 81(6): 773-780.
Liu, S., et al. (2014). “Hydrogen production via catalytic pyrolysis of biomass in a two-stage fixed bed reactor system.” International journal of hydrogen energy 39(25): 13128-13135.
Lund, H. (2007). “Renewable energy strategies for sustainable development.” Energy 32(6): 912-919.
McKendry, P. (2002). “Energy production from biomass (part 1): overview of biomass.” Bioresource technology 83(1): 37-46.
Momirlan, M. and T. N. Veziroglu (2005). “The properties of hydrogen as fuel tomorrow in sustainable energy system for a cleaner planet.” International journal of hydrogen energy 30(7): 795-802.
Muradov, N. and T. Veziroǧlu (2005). “From hydrocarbon to hydrogen–carbon to hydrogen economy.” International journal of hydrogen energy 30(3): 225-237.
Ni, M., et al. (2006). “An overview of hydrogen production from biomass.” Fuel processing technology 87(5): 461-472.
Nikolaidis, P. and A. Poullikkas (2017). “A comparative overview of hydrogen production processes.” Renewable and sustainable energy reviews 67: 597-611.
Parthasarathy, P. and K. S. Narayanan (2014). “Hydrogen production from steam gasification of biomass: influence of process parameters on hydrogen yield–a review.” Renewable energy 66: 570-579.
Rossmeisl, J., et al. (2005). “Electrolysis of water on (oxidised) metal surfaces.” Chemical physics 319(1-3): 178-184.
Steinberg, M. (2004). A Highly Efficient Combined Cycle Fossil and Biomass Fuel Cell Power Generation and Hydrogen Production Plant With Zero CO2 Emission. International Conference on Fuel Cell Science, Engineering and Technology.
Steinfeld, A. (2005). “Solar thermochemical production of hydrogen––a review.” Solar energy 78(5): 603-615.
Wiberg, N., et al. (2007). Lehrbuch der Anorganischen Chemie, 102. Aufl, Walter de Gruyter, Berlin.
Zakkour, P. and G. Cook (2010). “CCS Roadmap for Industry: High-purity CO2 sources.” Carbon Counts Company Ltd: UK.
Züttel, A. (2003). “Materials for hydrogen storage.” Materials today 6(9): 24-33.